KUKA Aerospace plans for growth with Michigan expansion
The project is the third in a series of current investments to expand the R&D, engineering and manufacturing footprint of KUKA's global aerospace group, based in Michigan.
STERLING HEIGHTS, MI, April 21, 2015 — KUKA Systems is expanding its facility in Clinton Township, MI, to support the further growth of its aerospace business. Ground-breaking is expected in early May. The project is the third in a series of current investments to expand the R&D, engineering and manufacturing footprint of KUKA's global aerospace group, based in Michigan.
KUKA already has opened a 29,000 sq ft facility in Everett, WA to support customers on the West Coast. The Everett facility is KUKA Systems' first US installation outside Michigan.
Earlier this month, KUKA officially opened a new R&D and production facility for advanced aerospace automation solutions in Le Haillan, France. That building has over 28,000 sq ft of floor space for production, engineering and other departments. Products manufactured there include end effectors, the functional units attached to a robot arm that perform specific production or logistical tasks like drilling, riveting, fastening, and positioning. KUKA also manufactures these end effectors in Michigan for US customers.
The KUKA Aerospace Group has been expanding rapidly by offering major airframe manufacturers assembly solutions based on assembly line principles as well as automated manufacturing tools and solutions.
"These investments are a response to the strong uptake of our technologies and solutions by major aerospace companies around the world," says Robert Reno, Group Vice President, KUKA Aerospace Group. "By working closely with them in the design and deployment of these concepts, we're helping change the way aircraft are assembled."
KUKA's US customers includes Boeing, Northrop Grumman, Gulfstream Aerospace and Bell Helicopter. KUKA has built a highly automated assembly line for Northrop Grumman to build center fuselages for the F-35 jet fighter. It also is building automated manufacturing systems for the Boeing 777 and 737-MAX programs. For Gulfstream, it is supplying tooling and mobile robotic platforms to help build its newest corporate jets, while it has supplied a complete assembly line for building Bell's new super-medium class commercial helicopter, the 525 Relentless. The European customer base includes Airbus, Dassault Aviation and Stelia Aerospace.
ABOUT KUKA SYSTEMS:
KUKA Systems, part of Germany-based KUKA AG, is an international supplier of engineering services and flexible automation systems for the Automotive, Aerospace, Energy, and Industrial Solutions segments. Some 5,800 employees worldwide work on ideas, concepts and solutions for automated production and the provision of products and services for virtually all tasks in the industrial processing of metallic and non-metallic materials. The range is marketed internationally via subsidiaries and sales offices in Europe, America and Asia. KUKA Systems had sales revenues of 1.28 billion euros for the 2014 business year. KUKA Systems North America LLC, based in Sterling Heights MI, is responsible for the North American business and the worldwide aerospace group. The Aerospace Group focuses on all aspects of tooling and assembly processes for aircraft manufacturing.
Featured Product
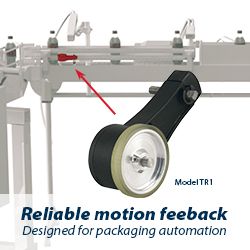
Model TR1 Tru-Trac
The Model TR1 Tru-Trac® linear measurement solution is a versatile option for tracking velocity, position, or distance over a wide variety of surfaces. An integrated encoder, measuring wheel, and spring-loaded torsion arm in one, compact unit, the Model TR1 is easy to install. The spring-loaded torsion arm offers adjustable torsion load, allowing the Model TR1 to be mounted in almost any orientation - even upside-down. The threaded shaft on the pivot axis is field reversible, providing mounting access from either side. With operating speeds up to 3000 feet per minute, a wide variety of configuration options - including multiple wheel material options - and a housing made from a durable, conductive composite material that minimizes static buildup, the Model TR1 Tru-Trac® is the ideal solution for countless applications.