Fonon Unveils Update to Laser Cutting Technology for Glass
Patented approach to cutting and scoring glass on a molecular level increases the material's edge impact strength by up to 5x.
Lake Mary, FL, March 21, 2016 (Newswire.com) - Fonon Corporation (OTC: FNON) today announced improvements to Zero Width Laser Cutting Technology, a non-contact method for cutting glass and other non-metallic, brittle materials on the molecular level. The advancements have direct applications in the semiconductor, flat panel, solar, and medical glass industries.
Zero Width Laser Cutting Technology uses a non-contact laser to create internal tensile forces greater then inter-molecular connections in glass or other brittle materials, effectively separating the material cleanly, without the debris, loss, and quality problems associated with traditional glass processing. Waste material is largely eliminated, and the approach works with all types of glass.
Recent refinements by Fonon allow products which incorporate Zero Width Laser Cutting Technology to achieve much deeper penetration of a precisely controlled micro-crack. The process creates high-speed scribe lines (up to 1 meter per second, depending on the material type and thickness) in a prearranged manner, with no molecules leaving the surface, dramatically improving the substrate separation process.
Edge impact strength increases when glass is cut by this process; the result is up to five times stronger than material cut by mechanical scribe and break methods.
"Both manufacturers and consumers benefit immediately," said Ben English, Chief Marketing Officer of Fonon Corporation. "Zero Width Laser Cutting Technology provides higher material strength for all types of glass, and less possibility of damage either at the factory or in the customers hand."
Cutting systems incorporating Fonons latest Zero Width Cutting Laser Technology are available immediately, in standalone systems, for the flat panel display, medical device, and precision optics industries.
For more information, see the Fonon blog entry, "What is Zero Width Laser Cutting Technology?" by following this link, or contact Fonon for more details.
About Fonon Corporation
Fonon designs laser-based material processing technologies for advanced industrial manufacturing and manufactures state of the art equipment utilizing those technologies. The company products empower manufacturers in the areas of application-specific 3D metal printing (additive manufacturing), and 2D and 3D laser cutting, marking and engraving applications (subtractive manufacturing). Our products and technologies are used today in every sector of any manufacturing industry from food and beverage to medical, aerospace and semiconductor. For more information, visit www.fonon.us.
Featured Product
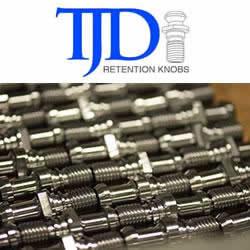
T.J. Davies' Retention Knobs
Our retention knobs are manufactured above international standards or to machine builder specifications. Retention knobs are manufactured utilizing AMS-6274/AISI-8620 alloy steel drawn in the United States. Threads are single-pointed on our lathes while manufacturing all other retention knob features to ensure high concentricity. Our process ensures that our threads are balanced (lead in/lead out at 180 degrees.) Each retention knob is carburized (hardened) to 58-62HRC, and case depth is .020-.030. Core hardness 40HRC. Each retention knob is coated utilizing a hot black oxide coating to military specifications. Our retention knobs are 100% covered in black oxide to prevent rust. All retention knob surfaces (not just mating surfaces) have a precision finish of 32 RMA micro or better: ISO grade 6N. Each retention knob is magnetic particle tested and tested at 2.5 times the pulling force of the drawbar. Certifications are maintained for each step in the manufacturing process for traceability.