Enhancing Equipment Reliability: Implementing XPump AI/ML Predictive Maintenance on DD Series Split Dual-Helical Dry Vacuum Pump DD255
In today's fast-paced industrial landscape, equipment reliability and operational efficiency are paramount. Pumps and motors are the lifeblood of many industrial processes, making their maintenance crucial for avoiding costly downtimes and repairs. The DD Series Split Dual-Helical Dry Vacuum Pump DD255 is no exception. Integrating XPump's AI/ML-based pump monitoring and predictive maintenance system can revolutionize how we manage these critical assets. In this blog, we will explore how XPump enhances equipment reliability and operational efficiency for the DD255 Dry Vacuum Pump.
The Importance of Predictive Maintenance in Modern Industry
What is Predictive Maintenance?
Predictive maintenance involves monitoring the condition of equipment and predicting when maintenance should be performed. This approach minimizes the risk of unexpected failures and extends the lifespan of machinery by addressing issues before they escalate. Unlike reactive maintenance (which occurs after a breakdown) or preventive maintenance (which follows a scheduled approach), predictive maintenance leverages real-time data to inform maintenance decisions, leading to significant cost savings and efficiency improvements.
The Role of AI/ML in Predictive Maintenance
Artificial Intelligence (AI) and Machine Learning (ML) technologies play a critical role in predictive maintenance systems. By analyzing vast amounts of data collected from equipment sensors, these technologies can identify patterns and anomalies that human operators might miss. This capability enables the prediction of potential failures and maintenance needs with high accuracy, ensuring that interventions are made only when necessary and before any major issues arise.
Introducing XPump: AI/ML-Based Monitoring for the DD255 Dry Vacuum Pump
What is XPump?
XPump is a state-of-the-art solution designed to provide real-time monitoring and predictive maintenance for pumps and motors. It utilizes advanced AI/ML algorithms to continuously track vital parameters such as vibration, temperature, and voltage. This continuous monitoring allows XPump to detect early warning signs of potential problems and optimize the performance of the equipment.
How XPump Enhances the DD255 Dry Vacuum Pump
The DD255 Dry Vacuum Pump is known for its robust performance in various industrial applications. However, like any mechanical system, it can suffer from wear and tear over time. XPump enhances the DD255 by providing:
Real-Time Monitoring: XPump continuously monitors the DD255's operational parameters, ensuring that any deviations from normal behavior are detected immediately.
Predictive Maintenance Alerts: By analyzing the collected data, XPump can predict when parts of the DD255 are likely to fail and notify maintenance teams weeks in advance.
Optimized Performance: With continuous monitoring and data analysis, XPump helps maintain the DD255 at optimal performance levels, reducing energy consumption and improving overall efficiency.
Reduced Downtime: By preventing unexpected failures and minimizing the need for unscheduled maintenance, XPump significantly reduces downtime for the DD255.
Cost Savings: The early detection of issues and optimized maintenance schedules translate into substantial cost savings on repairs and replacements for the DD255.
Key Features of XPump for DD255 Dry Vacuum Pumps
Turnkey Solution
XPump comes as a comprehensive solution that includes all necessary hardware and software components. This ease of integration ensures that you can start benefiting from XPump's capabilities without any significant changes to your existing infrastructure.
Universal Compatibility
One of the standout features of XPump is its ability to work with all types of pumps, exhausts, blowers, and motor-based devices, regardless of the manufacturer. This flexibility makes it an ideal choice for facilities with diverse equipment inventories.
Advanced Connectivity
XPump supports SECS/GEM and other connectivity protocols to integrate seamlessly with factory systems such as SCADA, MES, and ERP systems. This integration ensures that data from the DD255 and other equipment can be aggregated and analyzed holistically.
Cloud-Based and On-Premises Options
XPump offers both cloud-based and on-premises deployment options. Whether you prefer the scalability and ease of a cloud solution or the control of an on-premises setup, XPump can accommodate your needs.
Case Study: XPump in Action
To illustrate the impact of XPump, let's consider a case where XPump was implemented in a facility using the DD255 Dry Vacuum Pumps. Before XPump, the facility faced frequent, unexpected downtimes due to pump failures, resulting in significant production losses and maintenance costs.
After integrating XPump, the facility saw a dramatic reduction in downtime. XPump's predictive alerts allowed maintenance teams to address issues before they led to failures. The continuous performance optimization provided by XPump also reduced the energy consumption of the DD255 pumps, contributing to lower operational costs. Overall, the facility reported savings of over $500,000 annually thanks to XPump's capabilities.
Implementing XPump: Steps to Get Started
Step 1: Assessment
Begin with a thorough assessment of your existing equipment and maintenance processes. Identify the critical pumps and motors in your operations and evaluate their current performance and maintenance schedules.
Step 2: Integration Planning
Work with XPump's technical team to plan the integration of XPump into your system. This includes determining the best configuration for your specific needs, whether cloud-based or on-premises.
Step 3: Installation and Setup
Install the XPump hardware and software components. XPump's turnkey nature simplifies this process, minimizing disruptions to your operations.
Step 4: Training and Optimization
Train your maintenance and operations teams on how to use XPump effectively. Leverage XPump's data insights to optimize your maintenance schedules and improve equipment performance.
Step 5: Continuous Improvement
Regularly review the data and insights provided by XPump to continuously refine and improve your maintenance strategies. Stay proactive and adapt to any changes in your equipment's behavior.
Incorporating XPump's AI/ML-based monitoring and predictive maintenance system into your DD Series Split Dual-Helical Dry Vacuum Pump DD255 operations is a transformative step towards enhanced reliability and efficiency. By leveraging real-time data and advanced algorithms, XPump ensures that your equipment remains in peak condition, minimizing downtime and reducing costs.
Don't let your equipment's performance be a guessing game. Embrace the future of maintenance with XPump and keep your operations running smoothly and efficiently.
Contact us today to learn more about how XPump can transform your equipment maintenance practices. Visit our website to request a demo or speak with our experts. Let's take your operational efficiency to the next level with XPump's cutting-edge technology!
Featured Product
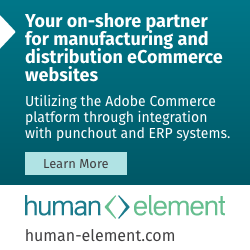