The Theory of Relativity in Control System Design
Distributed Control System (DCS) providers identify as a best practice pursuing a standardized approach to the configuration and control of Related Units within batch processes.
For most processors, the Distributed Control System (DCS) plays a critical role in operations and control. To maintain quality standards, the DCS software must provide a high level of accuracy to ensure that the mixtures of chemicals or ingredients are adequately controlled through each step in the process to produce the desired product and minimize quality inconsistencies.
Given that no two processes are alike, however, there are tremendous benefits to utilizing established standards and best practices that provide a consistent framework for the creation of the fundamental building blocks of the DCS - the Unit. In processing, a Unit is responsible for a specific action within the Master Recipe, such as heating, cooling, adding, blending, or separating material. Most batch processes consist of a "train" of such Units, where material is introduced in the first Unit and passed from Unit to Unit.
A blank sheet of paper
In many ways, designing a DCS application from scratch is like starting with a blank sheet of paper. There are infinite variables related to the type of equipment, the material being processed, the operator's actions, and the control system. As such, the DCS can be configured in almost any way imaginable, which can lead to a robust system that delivers precise and predictable control or could lead to lost product, process interruptions, and even safety issues when done poorly.
The DCS must, therefore, be designed based on defined standard methods with consideration of every aspect of the application within the context of the whole. This includes the structure of the database, initialization options, alarm management, logic standards, common loop design, and even naming conventions.
However, standardization also plays a key role in simplifying the formation, organization, and even software programming of the Units within the DCS.
This is where the concept of Unit Relativity comes into play. The goal is to design a fixed sequence for one Unit that can be executed on any number of similar Units. To accomplish this, there must be a consistent organization of relative Units with the same structure, sequence of actions, variables, and naming conventions.
The degree to which a single control operation can be used on multiple units depends on specific DCS capabilities. Some control platforms require a unique sequence for each Unit that can be copied and used for other Units. Other platforms adopt the concept of a "Unit Class" where control operations can be executed on any member of the class.
By applying Unit Relativity in either of these ways, DCS providers can greatly reduce the lifecycle costs of the application and help ensure uniform controls across all similar units.
It also aligns with the ANSI/ISA88 standards published by the International Society of Automation, which provides processors with standards and recommended practices for the design and specification of batch control systems including, among other stated goals, reducing the amount of software programming required.
The Birth of Unit Relativity
The concept of Unit Relative Operations was first introduced to the process control industry by EMC Controls with the D/3 DCS in 1982. Since then, more vendors have begun to offer support for this approach.
"Whether a system comes with built-in support for Units or whether they must be created from scratch, dividing a process into functional Units is an industry-standard approach to process control," says Robert M. Ard, Senior Advisor at Valmet . Valmet is a leading global developer and supplier of process technologies, automation, and services for the pulp, paper, energy, marine, and other process industries. In January of 2023, the company completed the acquisition of the popular D3 Control System from NovaTech Automation.
According to Ard, most DCS providers group equipment into Units and then design controls to operate those Units.
In fact, the S88 flexible batch standard requires the control system to be organized into Units. S88-based software solutions are designed to allow recipe creators or operators to modify recipe parameters, procedures, production schedules, batch start rules, equipment utilization, or to scale batch amounts more easily and at any time.
According to Ard, Valmet's D3 Control System has built-in support for Unit-based control. D3's Phase logic and the company's proprietary software, FlexBatch®, control the Units required to make the batch. To achieve Unit Relativity, each similar Unit in the D3 Control System is configured with identical contiguous structures, using the same types of devices, and in the same sequence of operations.
"D3 Unit Relativity allows Phase logic to be designed for a Unit Class and then executed on all Units derived from that class. This greatly reduces the number of Phases that must be designed, tested, and maintained for the life of the control system," explains Ard. "Since all similar Units execute the same control software, they all operate in exactly the same way. The result is fewer Phases to create and maintain and reduced variability across all Units."
Coordination Between Units
Ard adds that a well-designed DCS must also manage the coordination between Units even if Unit Relativity is applied.
"Most batch processes are a daisy chain of Units where the material starts in one and is processed to a certain point before it is moved into another Unit for further processing. So, although Units typically operate independently, the DCS design must address coordination between Units for tasks such as material transfers and so forth," says Ard.
With FlexBatch, each Unit has an associated Unit Recipe within the larger Master Recipe required to make the batch. The Unit executes a series of Operations within the Unit Recipe where each Operation is comprised of one or more Phases. Each Phase represents a sequential control program that is designed to perform a specific task, such as control opening and closing of valves, increasing temperature, pH control, or addition of materials. FlexBatch allocates and deallocates equipment as needed.
When designing Unit to Unit transfers, it is important to account for potential equipment failures or other runtime issues that might suspend the material transfer. The interfaces should be designed so operators can resume the transfer on a single screen that controls only the Unit that has the problem. Designs that require operator action on both Unit screens to resume a transfer should be avoided.
It is also good practice to design Units using States to address common situations, such as a "Maintenance State" to augment lockout/tagout procedures. Another common structure is a "Hold State," where the process is brought to a safe state should operators need to respond to abnormal situations. Units should also support a "Fail State" if equipment failures prevent normal processing.
Given the essential role the DCS plays in ensuring the quality and consistency of operations in various industries, the primary goal of every control application should be robust and predictable control under all process conditions. To accomplish this, the best results are achieved when the process control application follows the same best practices and techniques.
The concept of Unit Relativity offers a solution for simplifying DCS formation and organization while reducing costs. By applying uniform controls across all related units, DCS providers can ensure a consistent and efficient process that aligns perfectly with ANSI/ISA88 standards.
"Following the same configuration best practices and applying it to related Units reduces the risk of errors and results in a more robust application," says Ard.
Ard is writing a comprehensive guide to control system design to assist processors in this endeavor, tentatively titled "How to D3." The book is expected to be published in 2024.
Among other general guidelines control system engineers should know or consider when tackling any DCS project, the book elaborates on the critical role of standardization and gives specific examples of Unit-Relativity and programming specific to the Valmet D3.
For more information, visit www.valmet.com or call 410-753-8300.
Featured Product
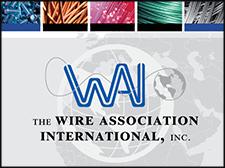
The Wire Association International (WAI), Inc.
The Wire Association International (WAI), Inc., founded in 1930, is a worldwide technical society for wire and cable industry professionals. Based in Madison, Connecticut, USA, WAI collects and shares technical, manufacturing, and general business information to the ferrous, nonferrous, electrical, fiber optic, and fastener segments of the wire and cable industry. WAI hosts trade expositions, technical conferences, and educational programs.