The Production Process Of Automotive Fuel Injection Lines
The fuel injection lines help to deliver the fuel that is needed from the fuel tank to the fuel injectors. Any time that you crank the car, the fuel lines will have to deliver the gas that is needed for the combustion process.
The production process of automotive fuel lines includes the preparation of raw materials, processing and moulding, and quality inspection, etc.
1. Material preparation: choose suitable raw materials, generally oil-resistant, high-temperature-resistant rubber materials. Mix the raw materials according to the proportion, add processing aids, and pre-treatment by crushing, screening and other processes.
2. Rubber mixing: feed the mixed raw materials into the rubber mixing machine for mixing. The purpose of mixing is to fully mix the raw materials which be reacted with processing aids to give the rubber a certain elasticity and resistance to oil and high temperature.
3. Extrusion moulding: the mixed rubber is fed into the extruder for extrusion moulding. The extruder heats up the rubber, pressurises it and extrudes it through the mould to form the initial shape of the fuel lines.
4. Cooling and solidifying: The extruded fuel line is rapidly cooled by means of cooling water to allow the rubber to solidify quickly.
5. Surface finishing: The solidified fuel line is subjected to surface treatment, such as deburring, decontaminating and polishing, to improve the appearance quality.
6. Quality inspection: The quality inspection of the fuel line is carried out through optical, physical and chemical methods to check the dimensions, physical properties and oil resistance of it.
7. Packaging: Qualified fuel lines are packaged and shipped out of the factory, and are ready for delivery according to the specified storage conditions.
It is the general production process of automotive fuel lines above, the specific process and process parameters will vary according to different manufacturers and product requirements.
Featured Product
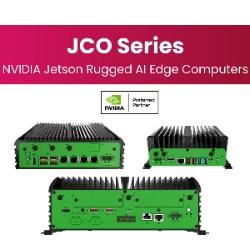
JCO Series: NVIDIA Jetson Rugged AI Edge Computers
The JCO Series is a line of NVIDIA Jetson rugged AI edge computers. Unlike standard CPUs, the JCO series employs NVIDIA Jetson-Orin modules, introducing an ARM-based SOM (System-on-Module) architecture with CPU, GPU, and RAM on the same module. This integration brings about significant AI performance right to the edge, coupled with a rugged, fanless design suitable for enduring extreme environments. This series highlights low power consumption (7-60 watts) yet delivers high AI performance up to 275 TOPS, a feat difficult for typical x86 solutions to match. The integration of customizable EDGEBoost IO technology and out-of-band remote management features ensures advanced connectivity and maintenance capabilities, solidifying the JCO Series as an essential solution for mission-critical deployments such as AGV & AMRs, security & surveillance, industrial automation, and industrial IoT. With UL listed, E-Mark, FCC, and CE certifications, the JCO Series meets the highest industry standards for ultimate safety and reliability.