A No-Cost Model to Close the Manufacturing Digital Divide. You Read that Right.
The majority of U.S. factories – the small to medium-sized businesses (SMBs) that make up 98 percent of our supply chain – continue to rely heavily on manual tools that are difficult to maintain, like spreadsheets and pen and paper, for managing their operations.
Almost every industry - from retail, to finance, healthcare, and more - is embracing digitization to streamline operations, harness data insights, and deliver more value to its business and employees.
However, manufacturing, despite being one of the biggest economic drivers in the country, has been left behind. How come? The majority of U.S. factories - the small to medium-sized businesses (SMBs) that make up 98 percent of our supply chain - continue to rely heavily on manual tools that are difficult to maintain, like spreadsheets and pen and paper, for managing their operations.
"Follow Bob around for two weeks to learn the process" is how operator training is often handled. Standard work along the assembly line is frequently documented in a binder, leaving operators to guess the ideal method to create the end-product. There's a myriad of challenges that smaller factories face, and singularly, not one is enough to warrant an independent solution.
The need to digitize is existential for the modern manufacturing industry. High-profile factory errors are dominating headlines, and the industry will have a shortage of 2.8 million workers in the next three years. Without digitization in the most basic form, the American supply chain network remains unproductive - operating 20 to 40 percent below industry standard targets.
What's stopping factories from adopting the latest manufacturing tech? Lack of budget is one of the most common reasons. The high price and complex onboarding & installation process associated with factory floor technology has long stymied small and mid-size factories from initiating their digitization journeys. Even industry-standard free trials aren't worth the headache, as the majority of digital systems take longer than the standard 30 days to implement.
To restore U.S. manufacturing as a global leader in productivity, bold changes are required. That's why starting today, all manufacturers will be able to use Pico MES' digital work instruction suite of tools for free. Every manufacturer who signs up will receive a cloud-based instance with capabilities to build worker guidance instructions, create digital process flows, and assign stations. The only restrictions will be on the number of stations and operators (we're not a charity, larger factories can pay a nominal fee), and the data tools that drive up our costs.
This is not a free trial with a time limit. This no-cost model supports our mission of modernizing the supply base and taking cost out of the equation.
The Method Behind Our Madness
Our goal is to make the first step of a factory's digitization journey as frictionless and scalable as possible without leading to a dead end. Digital work instructions are a key component when initiating this transformation. By offering these solutions for free, we are furthering our mission to make factory modernization standard within the sector.
The typical 30 day free trial window is rarely enough time for a factory to establish value - not because value is difficult to realize, but because factory leaders are often distracted with daily firefighting and are championing multiple projects at once. Offering a no-cost solution, instead, makes it easier for factories to prove out the improvements in training time and increase output without the barrier of an upfront investment.
Digital transformation is only hard if you make it hard
It always starts with a first step. Once they've created a strong digital foundation, teams can catapult, accelerate, and actualize a more modern and efficient factory future. Every five minute gain from using digital solutions - from answering yet-another operator question, to reworking a part that was built incorrectly - can be reinvested into other factory operations, continuing a steady drumbeat of factory improvement.
One of the easiest ways to drastically reduce human variability is to give all operators a set of standardized work instructions with images and videos to guide their step by step processes. This then becomes interactive operator guidance that's engaging and enjoyable while impacting retention. It becomes a teacher, ensuring the right information is present at the right time. Pico users then tie those instructions into connected tools and business systems, further amplifying gains and ensuring true continuous improvement.
With products constantly evolving and labor forces changing, empowering manufacturers with strong operator guidance is a must to ensure quality assurance and efficiency. Moreover, digital tools are essential as the industry attempts to attract a Gen Z and millennial workforce amid an existential labor shortage. The next generation of digital-native factory employees expects a modern work environment, and smart factories are essential to attracting and retaining these workers.
What's Holding You Back?
By digitally connecting workers with the tools they use everyday, factories can improve the operator experience to attract and retain new factory floor employees.
When workers are happier and know how to do their jobs clearly and effectively, factories can reduce production errors while maintaining efficiency under heightened scrutiny from high-profile manufacturing errors.
Moreover, stronger factories make for stronger local economies, as small manufacturing towns attempt to revitalize in the age of offshore manufacturing.
Anybody can get started at https://www.picomes.com/tryforfree. We've essentially eliminated price as an excuse, and now the only standing defense is simply "I don't care enough to improve."
So what are you waiting for?
Featured Product
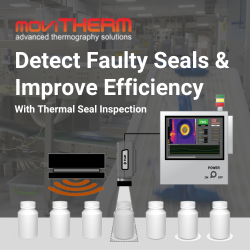
Thermal Seal Inspection for Improved Quality and Efficiency
MoviTHERM's Thermal Seal Inspection (TSI) solution provides precise and reliable detection of defects in a variety of packaging types, including pouches, bags, blister packs, bottle caps, and more. By detecting defects in your packages, the TSI solution helps increase efficiency in your production line and ensures top-quality packaging is delivered to your customers every time. With state-of-the-art technology and an experienced team, MoviTHERM is dedicated to delivering accurate inspection solutions and peace of mind to its clients. Contact MoviTHERM today to learn more about their thermal seal inspection solution.