Greater interoperability through unified machine vision standards
Standardization is particularly beneficial for machine vision applications, where many different components interact. Customers benefit from easy-to-use, seamless applications, reducing complexity and increasing process efficiency.
Solutions and products for the industry need to be highly interoperable to provide maximum benefit to users. Achieving this goal is primarily possible through common standards and interfaces. These also facilitate smooth collaboration between different manufacturers, leading to a lively exchange of know-how and enriching the market. Moreover, unified standards offer an added level of flexibility as they counteract the dependency on proprietary solutions. Standardization is particularly beneficial for machine vision applications, where many different components interact. Customers benefit from easy-to-use, seamless applications, reducing complexity and increasing process efficiency.
Developing common standards usually requires a lot of work from companies: They must assign experienced internal experts to relevant committees and engage in related communities and associations. This ties up valuable personnel resources and incurs high costs. Additionally, the coordination processes until the final adoption of new standards can extend over a very long period, consuming energy and resources. Companies therefore carefully consider whether to invest personnel, time, and monetary resources in the development of unified standards. Some manufacturers might focus more on developing their own proprietary solutions and products.
This strategy appears promising in the short term: Companies often aim to clearly distinguish themselves from the competition and position themselves in the market with a unique selling proposition. However, this approach should be handled with caution, as it leads to the development and establishment of isolated solutions. This brings disadvantages for all parties involved, ultimately affecting the customers: While manufacturers may quickly have a functioning system, proprietary interfaces can limit customers' freedom of choice in the long term, preventing the systems from succeeding in the market. This lacks future viability, and development costs may need to be written off. Moreover, such isolated solutions regularly contribute to the fragmentation of the market and industry.
Cooperation instead of isolated solutions
Therefore, a strategy of cooperation focusing on the development of seamless interfaces and common standards is more beneficial for companies. Although such an open approach requires a certain level of commitment and is associated with effort, it offers numerous advantages: It paves the way for seamless interoperability between various systems and solutions. As these communicate in a standardized language, they can be flexibly interchanged as needed. This stimulates competition and ultimately leads to more mature, well-thought-out products. Users, in particular, benefit. They have more options to compare solutions and select the best offer in the market. This leads to more choice, flexibility, and cost transparency, and increases resilience, as dependency on individual suppliers and their availability is reduced.
Moreover, a high degree of standardization promotes cooperation between experts, allowing them to exchange their knowledge and experiences. This creates a "brain pool," serving as an important driver of technological progress. Not only established manufacturers benefit. Young companies can also use existing standards to develop seamlessly integrable solutions and bring them to market. Standards are not an obstacle for developing projects individually; rather, they offer a basis for innovations and product improvements, which help all the actors involved. For example, developers can rely on existing and proven interfaces instead of programming them from scratch, allowing innovative products to be brought to market more quickly and established there in the long term.
Common standards for seamless machine vision processes
In industrial image processing (machine vision), standards and interfaces are increasingly used. The most important role is played by technical industrial standards, whose development and adoption are the responsibility of associations and companies. Important technical industry standards in the machine vision environment include standards for image acquisition, such as GigE Vision. This ensures a seamless connection of image acquisition devices like industrial cameras or sensors to network infrastructures through a Gigabit Ethernet interface.
The GenICam (Generic Interface for Cameras) interface can also be used to integrate cameras seamlessly, decoupling the cameras' interfaces from specific application programming interfaces. MVTec, a leading provider of standard software for machine vision, has significantly contributed to the development of the GenICam interface: The company has independently programmed the GenICam GenTL Producer Framework and made it available for general use. In this context, the production-ready code is available free of charge to the entire GenICam community and its customers.
Moreover, in machine vision, standards for seamless process communication are of central importance. OPC UA (Open Platform Communications Unified Architecture), for instance, ensures smooth data transfer between components from different providers. This paves the way for seamless compatibility with all conceivable platforms and operating systems. As a superordinate framework, OPC UA sets the standard for a common language through which various system worlds can exchange and communicate data. This makes it possible to integrate various applications for industrial automation seamlessly.
Deep learning standards still lack market maturity
Technologies based on artificial intelligence (AI), particularly deep learning, which relies on artificial neural networks (Convolutional Neural Networks / CNN), are becoming increasingly important for the entire industrial environment and thus for machine vision. Common standards are being created for this purpose, though they are still in the early stages of development. One of the first initiatives in this field is the Open Neural Network Exchange (ONNX), an open format for representing machine learning models, already supported by some frameworks. However, due to the multitude of frameworks, libraries, and methods in use, this standard is highly fragmented. Thus, it cannot yet fully cover productive operation in an industrial context.
How can companies actually benefit from the development of common standards and interfaces? This becomes particularly clear in light of the new challenges the industry faces: The economy is increasingly under pressure due to ongoing supply chain disruptions, heightened geopolitical risks, the decoupling of Chinese and American markets, and a rapidly accelerating shortage of skilled workers. This is also accompanied by continuous changes in customer expectations and requirements. To increase resilience against these factors, manufacturing companies must respond with a profound transformation of their processes.
Standardization paves the way for seamless process integration
Customer requirements have changed significantly in recent years. Factors include increased awareness of climate change, geopolitical risks leading to adjustments in supply chains, and volatile energy prices. As a result, price sensitivity increases, transparency and sustainability become more important, and finally, both flexibility and usability increasingly gain significance. The manufacturers' response to these challenges is adaptive manufacturing. Process integration plays a crucial role here. At this point, common standards and interfaces are particularly beneficial, as they significantly facilitate the integration of various components into an application. This also applies to industrial image processing. For it to fully leverage its advantages and pave the way for seamless factory automation, machine vision components must be easily integrated into industrial value-added processes and the corresponding technologies. It is essential that the various levels of industrial production, such as sensors, programmable logic controllers (PLCs), SCADA systems, manufacturing execution systems (MES), and enterprise resource planning (ERP) solutions, communicate seamlessly and exchange data. Common norms and standards like OPC UA are indispensable for this.
An example of successful process integration in the industrial environment is the seamless integration of machine vision technologies from MVTec into Siemens' Industrial Edge Ecosystem. Following the principle of an app store, users can select the "apps" relevant to them within the Siemens platform and add them to their application. Industrial Edge provides a software infrastructure for central hardware management, scalable software rollout, and cloud connectivity. Through a standardized connectivity solution, centered around the Industrial Edge Databus (an MQTT broker), applications can be quickly and easily deployed. MVTec Software GmbH offers the "Anomaly Detection for Visual Inspection" app. This allows customers to implement visual surface inspection and optical quality control within the Siemens Industrial Edge platform based on deep learning. This significantly reduces complexity and lowers barriers, enabling customers to integrate imaging solutions into their machines and production plants easily. The "Anomaly Detection" application also supports the use of cameras. In this context, the "Anomaly Detection" application also supports the use of cameras according to the GigE Vision standard within the Industrial Edge Ecosystem.
Conclusion
Common standards and interfaces, especially in the machine vision segment, are the key to unlocking seamless interoperability between various systems and technologies. This primarily benefits customers: They gain from applications that are easy to integrate and can utilize the best technologies available in the market to meet their specific needs. As a result, companies can optimize their processes, increase productivity, and save costs.
About MVTec Software GmbH
MVTec is a leading manufacturer of standard software for machine vision. MVTec products are used in a wide range of industries, such as semiconductor and electronics manufacturing, battery production, agriculture and food, as well as logistics. They enable applications like surface inspection, optical quality control, robot guidance, identification, measurement, classification, and more. By providing modern technologies such as 3D vision, deep learning, and embedded vision, software by MVTec also enables new automation solutions for the Industrial Internet of Things aka Industry 4.0. With locations in Germany, the USA, France, China, and Taiwan, as well as an established network of international distributors, MVTec is represented in more than 35 countries worldwide. www.mvtec.com
Featured Product
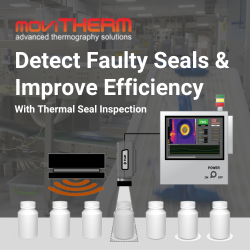