JD Manufacturing Boosts Fryer Output 20%, Reduces Fuel Use & Environmental Impact with Bison® Blower & Integration Support
Productivity and efficiency are paramount in the highly competitive snack food production industry. JD Manufacturing, Inc (JDM) in Pine Bluffs, WY, stands out as a leader with its high-performance automatic batch fryers, which are engineered specifically for kettle chip production. The batch frying process imparts kettle chips, whether made from potatoes, sweet potatoes, parsnips, carrots, or beets, with their distinctive premium texture and taste. With approximately 160 systems operational across five continents, JDM has established a significant global footprint. JDM's fryers feature an innovative heat exchanger design that enables high production capacity. However, this advanced design places substantial demands on the blower.
Industry Leading Power Density
To meet these demands, JDM enhanced its systems with the Nautilair® 12.3" High Energy Blower by Bison®, which is known for its industry-leading power density. This blower was specifically developed to meet customer needs for greater power without increasing the blower size.
The Situation and Opportunity
With its innovative heat exchanger design, JDM's high-capacity batch fryer, the JD500CXI, is engineered to produce 500 lbs. of chips per hour. This advanced design injects a flame into an 8-inch stainless steel exchanger tube extending into the oil bath, where the chips are fried, eventually releasing air through an exhaust flue.
To maximize heat reclamation efficiency, 2-inch cross tubes enlarge the surface area, and static mixers inside the tubes prevent laminar flow. These features are very effective in capturing additional heat from the air; however, they also increase back pressure, causing the blower to work considerably harder.
JDM systems utilize direct-fired high-efficiency burners sourced from a specialized manufacturer. The burner series is specifically designed for firing immersion tubes in liquid tanks. The standard blowers included with these burners generally support the 500 lbs. per hour performance, but they struggle when the flue system does not meet JDM's specifications.
For instance, despite JDM's recommendation that the exhaust flue contain no more than two 90-degree direction changes, an architect designed an exhaust flue for one system with a total of 315 degrees in directional changes. This configuration resulted in significant back pressure, placing additional demands on the blower.
The Solution
To address this challenge, JDM sought a significantly more powerful blower that could seamlessly integrate with their existing fryer system. This new blower had to overcome the back pressure created by the heat exchanger design and maintain high performance even with suboptimal exhaust flue configurations.
JD Manufacturing required a blower that met several critical constraints: Retain the same footprint to fit in the existing enclosure and avoid altering the system size. Ensure compatibility with the existing 480V, 3-phase power setup. Withstand the harsh conditions of a food production environment, including exposure to moisture, oil-contaminated air, and aerosolized caustic substances.
According to Joshua Smith, Controls Engineer at JDM, "Our team anticipated that by replacing our three-phase AC motors with brushless DC motors, we could significantly increase power within the same space."
The Nautilair blower, featuring Neodymium magnets, operates more quietly and efficiently. The design of the blower's eight backward-curved fins further boosts performance, reduces noise, and maintains effective cooling.
Smith remarked, "The power density is astounding. We upgraded from a 1 HP AC motor to a 7.5 HP DC motor, all within the same space." He also emphasized that the new blower integrated seamlessly into their existing system, requiring no modifications to the enclosure, power supply, or other components. Since its installation, the Nautilair blowers have operated flawlessly.
One issue arose when the induced voltage from the fryers' ignition transformers, which convert 120-volt power to 6000 volts to ignite the burners, interfered with the electronics of the Nautilair BLDC drive. This issue was resolved through collaborative troubleshooting with JDM and Bison engineers by electrically isolating the ignition transformers.
During the investigation, Bison applications engineers recommended enhancing the blowers with Bison's upgraded silicone electronics coating to extend their lifespan in harsh operating conditions. Through this collaborative effort, the Bison team released a new model specifically designed to meet these demanding requirements.
Inspiration - What's Next?
An important advantage of the Nautilair blowers is their BLDC controllers that allow for the modulation of blower speed.
Smith highlights that "this innovation significantly enhances our fryers, providing precise control at both low and high flame levels, as well as during pilot conditions. This results in substantial financial benefits for our customers through reduced fuel consumption and increased efficiency, all while minimizing environmental impact.
"We are planning the integration of Nautilair blowers into our smaller units, aiming to extend these benefits across our entire product line. This strategic move underscores our commitment to delivering high performance, environmentally conscious solutions that meet the evolving needs of our customers," stated Smith.
The Results
The seamless integration of Bison's Nautilair 12.3" Combustion Blowers, with its remarkable power density, has enabled JD Manufacturing to exceed their high-performance standards, ensuring efficient production.
Even with installation that has the complex exhaust flue configuration with the 315-degree directional change, the switch to the Nautilair blower has significantly increased air pressure, boosting production to 585 pounds of kettle chips per hour — a 17% improvement. Other installations are producing 600 pounds per hour.
"The power density of the Nautilair blowers has made a huge difference for our customers," emphasizes Smith. "It empowers them with significantly higher productivity, reliability, and yield in their operations."
Learn more about the JD Manufacturing automatic batch fryer here: https://jdmanufacturinginc.com/automatic-batch-fryer/
To learn more about how a similar collaboration with Bison can help you design more efficient products, visit this Bison landing page: https://info.bisonametek.com/bison-food-beverage-motors-blowers
Featured Product
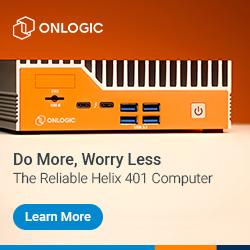