What is CNC Machining? Working Principles and Advantages
CNC (Computer Numerical Control) machining is an important automated machining technology in modern manufacturing. CNC machining enables the machining of parts with high precision, high efficiency and complex shapes by controlling the movement of the machine tool through a computer programme.
In this article, the basic concept of CNC machining, the working principle, the main advantages and practical applications will be introduced in detail.
1. Basic Concept of CNC Machining
CNC machining is a technology that uses a digital control system to automatically control machine tools. Precision machining of metals, plastics, wood or other materials is achieved through pre-written CNC programmes (e.g. G-code and M-code) that control the machine's parameters such as tool paths, cutting speeds and feeds. CNC machine tools include CNC milling machines, CNC turning machines, CNC grinding machines, and many other types that are capable of performing a wide range of machining tasks such as cutting, drilling, milling, turning and grinding.
2. Working Principle of CNC Machining
The working principle of CNC machining can be summarised in the following steps.
â‘ Design & Programming
First, engineers use computer-aided design (CAD) software to create a three-dimensional model of the workpiece. The design model is then converted by computer-aided manufacturing (CAM) software into CNC codes (e.g., G-codes) that contain detailed information on machining paths, cutting parameters, and so on.
â‘¡ Data Transmission
The written CNC programme is transferred to the control system of the CNC machine via a data transfer interface (e.g. USB, Ethernet, etc.). The control system reads and interprets these codes to generate control signals that drive the various moving parts of the machine.
â‘¢ Processing Execution
CNC machine tools automatically plan and execute tool paths according to CNC programme instructions. The moving parts of the machine tool (such as spindle, table, etc.) under the control of the CNC system, according to the predetermined trajectory of the movement, to complete the cutting, drilling, milling, turning and other operations on the workpiece.
â‘£ Testing & Adjustment
During the machining process, the CNC system monitors in real time the position of the tool and the workpiece, the cutting force and other parameters, and makes adjustments when necessary to ensure machining accuracy and quality. Some advanced CNC machines are also equipped with online measurement and feedback systems that allow real-time inspection and correction during machining.
3. Main Advantages of CNC Machining
CNC machining offers the following significant advantages over traditional manual machining.
â‘ High Precision & Consistency
CNC machining enables micron-level machining accuracy and ensures consistency from one part to the next. This is particularly important for products that require high precision and consistency, such as aerospace components and medical devices.
â‘¡ High Efficiency & Automation
CNC machining can be run continuously and automatically, dramatically increasing productivity. Especially in mass production, CNC machines can perform machining tasks unattended and with less human intervention.
â‘¢ Complex Shapes Processing
CNC machining makes it easy to perform complex curved surfaces and shaped structures, which are difficult to achieve with traditional manual machining. CNC machines are capable of multi-axis simultaneous machining, enabling the machining of arbitrarily complex shapes in three-dimensional space.
â‘£ Flexible Production
CNC machining has a high degree of flexibility, can quickly adjust the machining parameters and procedures, to adapt to different batches and multiple varieties of production needs. This makes CNC machining particularly suitable for the modern manufacturing industry in the multi-species, small batch production mode.
4. Practical Applications of CNC Machining
CNC machining is widely used in various industries, and the following are a few examples of typical applications.
â‘ Aerospace
The aerospace sector requires a high degree of precision and complexity in parts. CNC machining is capable of machining complex surfaces and high-precision holes through multi-axis simultaneous technology to meet the stringent requirements of aerospace components.
â‘¡ Automobile
CNC machining is used in automotive manufacturing for machining engine parts, body structure parts and moulds. CNC machining allows for efficient mass production, ensuring quality and consistency of each part.
â‘¢ Medical Device
Medical devices have extremely high requirements for precision and surface finish. CNC machining enables the precision machining of complex medical device parts such as artificial joints, surgical instruments and implants, ensuring high product quality and reliability.
â‘£ Renewable Energy
In the energy industry, particularly in the manufacturing of renewable energy equipment, CNC machining technology is used to produce turbine blades for wind power generation and frame structures for solar panels. These applications require materials with high strength and resistance to environmental attack, and CNC machining ensures that these parts meet the required specifications.
5. Trends in CNC machining
With the continuous progress of science and technology, CNC machining is developing in the direction of intelligence, networking and flexibility. The future of CNC machining will adopt more AI and IoT technologies to achieve adaptive machining, autonomous decision-making and remote monitoring to further improve machining efficiency and quality.
CNC machining, as an important part of modern manufacturing technology, has been widely used in various industries for its high precision, high efficiency and flexibility. As technology continues to advance, CNC machining will continue to evolve, driving manufacturing in the direction of greater intelligence, automation and efficiency. Understanding and mastering CNC machining technology not only improves the competitiveness of your business, but also promotes the overall progress of the manufacturing industry.
Featured Product
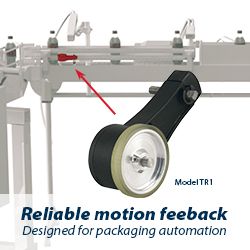
Model TR1 Tru-Trac
The Model TR1 Tru-Trac® linear measurement solution is a versatile option for tracking velocity, position, or distance over a wide variety of surfaces. An integrated encoder, measuring wheel, and spring-loaded torsion arm in one, compact unit, the Model TR1 is easy to install. The spring-loaded torsion arm offers adjustable torsion load, allowing the Model TR1 to be mounted in almost any orientation - even upside-down. The threaded shaft on the pivot axis is field reversible, providing mounting access from either side. With operating speeds up to 3000 feet per minute, a wide variety of configuration options - including multiple wheel material options - and a housing made from a durable, conductive composite material that minimizes static buildup, the Model TR1 Tru-Trac® is the ideal solution for countless applications.