Benefits and Challenges of Manufacturing Assembly Line Automation
Let's dive into the world of manufacturing assembly line automation and discover how it's shaping the future of production.
Automation of manufacturing assembly lines has become a vital driving force in today's industry.
Let's dive into the world of manufacturing assembly line automation and discover how it's shaping the future of production.
What is Manufacturing Assembly Line Automation?
Manufacturing assembly line automation is a way of using machines and technology to do the work that humans used to do. In an assembly line that is automated, a machine or robot handles things that are done repeatedly and in a large quantity, to make the production process more efficient. This automation can range from simple machines that perform a single function to more sophisticated systems that can be controlled by advanced software.
There are three main types of automation:
- Fixed Automation: The type of automation is mostly designed to high-volume production and is typically rigid and highly specialized for a particular task like in the automotive industry.
- Programmable Automation: This is the more flexible type of system which can be programmed for batch production and can be reconfigured for different tasks.
- Flexible Automation: A type of system that can quickly change from one product design or task to another, may be suitable even with minor manual intervention, and is preferred in industries where versatility is needed.
Current automotive, electronics, and pharmaceuticals are the leaders in the implementation of manufacturing assembly line automation, which is very beneficial to them in terms of increasing their operational efficiencies and scaling their operations internationally.
Key Benefits of Manufacturing Assembly Line Automation
Increased Efficiency and Speed
Assembly line automation is without a doubt the most impressive achievement of robotics. Machines are successful in doing work consistently time after time without taking breaks due to the fatigue that affects people. Moreover, automated systems can execute repetitive tasks error-free, which means postponement of activities due to human factors or fatigue is eliminated. As an illustration, firms that have utilized automation are now faster. They are thus able to meet market demand more efficiently with a maximum speed increase of up to 30%.
Consistent Quality and Reduced Error Rates
Automation solutions guarantee the same quality for every product produced, thereby resulting in fewer defects and higher consistency. Nevertheless, manual workers are a good deal but can still have a dimension of change in accuracy due to tiredness or just careless mistakes. On the other hand, automated machines adhere to specific requirements, thus, every product is the same. As such, the clients' orders are treated with downsized errors, lesses waste, and, consequently, more…are more pleased.
Cost Savings in the Long Run
Even though the automation costs at the beginning stage are mainly high, the gains in the long term are commonly acknowledged. Through machines that supplant the laborers in tasks that are repetitive and time-consuming, it is possible to decrease the labor costs in favor of taking strategic roles by human workers. Furthermore, companies are now able to save millions of dollars on materials as well as rework through better efficiency and, in turn, decrease errors. According to the McKinsey (2017) study, the organizations that went for full automation have experienced a new automatized environment with cost savings of around 20%.
Enhanced Worker Safety
Automation is a key point in making the worker's protective environment safer which leads to better worker safety. As part of their duties, workers in various industries often find themselves exposed not only to a hazardous environment but also to a machine that can injure them. Companies can achieve this by automating some of these tasks, thereby, minimizing the risk of injuries and, thus, protecting its workers. As the Occupational Safety and Health Administration (OSHA) shows, through the integration of automation, automated industries have seen a significant drop in workplace injuries.
The Challenges of Manufacturing Assembly Line Automation
High Initial Investment
One of the most significant hurdles to adopting manufacturing assembly line automation is the high upfront cost. The purchase and installation of automated systems, robotics, and advanced software require a substantial financial commitment. Smaller businesses, in particular, may find it challenging to justify this expenditure without clear visibility into long-term returns. However, while the initial costs may be steep, companies must view this as a long-term investment that will pay off in terms of efficiency and reduced operational costs.
Job Displacement and Workforce Transition
Automation can lead to job displacement, particularly for workers performing repetitive tasks that machines can easily handle. This challenge often sparks concern over job security in industries where automation is rapidly growing. However, the focus should shift to retraining and upskilling workers for more complex, strategic roles that machines cannot fulfill. As technology evolves, workers skilled in managing, programming, and maintaining automated systems will become invaluable assets.
Maintenance and Technical Expertise
Another challenge companies face with manufacturing assembly line automation is the need for technical expertise. Automated systems require regular maintenance and troubleshooting to avoid downtime. Companies will need to invest in training or hire specialized technicians to handle these systems. If a machine breaks down, it could cause production delays, negatively impacting output. Ensuring that proper support systems and personnel are in place can mitigate these risks and keep operations running smoothly.
Flexibility and Customization Limitations
Despite the many advantages of automation, certain systems may lack the flexibility needed for more customized or short-run production processes. Fixed automation systems, in particular, are designed for high-volume, repetitive tasks, making it difficult to adapt to new product designs without significant reconfiguration. Companies that require frequent changes in their production lines might find it challenging to strike a balance between automation efficiency and flexibility.
Final Words
Manufacturing assembly line automation offers incredible benefits, but it also comes with its challenges. As companies embrace automation, they experience increased efficiency, better product quality, and enhanced worker safety. However, challenges such as high initial costs, job displacement, and the need for technical expertise must be addressed to ensure a successful transition.
To thrive in this evolving landscape, businesses must strike a balance between automated systems and human labor, utilizing technologies like collaborative robots (cobots) and investing in workforce training. Looking to the future, innovations in AI, machine learning, and IoT solutions will continue to push the boundaries of what automation can achieve, making the next era of manufacturing both exciting and transformative.
Whether you're just starting or scaling up, understanding these benefits and challenges will give you a compet
Featured Product
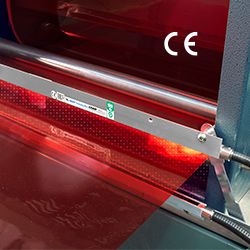