MVTec at the SEMICON Europa trade fair: Machine vision as a key technology for semiconductor manufacturing
• The slogan of the trade fair appearance "Machine Vision | Level up your speed and accuracy" addresses the challenges in semiconductor production • The quality assurance and alignment applications will be a particular focus at the MVTec booth
Munich, October 7, 2024 - MVTec Software GmbH (www.mvtec.com), a leading global provider of machine vision software, will be exhibiting again this year at SEMICON Europa in Munich, taking place from November 12 to 15, 2024. In hall 2, booth C2100, MVTec will be showcasing the benefits of machine vision technology for semiconductor and electronics manufacturing. "Machine vision is a key technology in modern semiconductor manufacturing. It improves both precision and efficiency throughout the production process, while also helping to reduce waste. Its applications range from seamless tracking and precise positioning to automated quality inspection across the entire process chain. With our extensive range of technologies and solutions, we are able to support the entire production process, from front-end to back-end. That's why we've chosen the slogan for our presence at SEMICON Europa: ‘Machine Vision | Level up your speed and accuracy,'" explains Klaus Schrenker, Business Development Manager at MVTec.
Focus: Quality assurance, positioning, and alignment in images
Semiconductor production involves hundreds of highly automated steps, offering numerous opportunities to leverage machine vision even more effectively. Key applications include identification, alignment, positioning, measurement, and defect detection. MVTec will be demonstrating how their software products, MVTec HALCON and MVTec MERLIC, can provide specific support in these areas through two demos at their booth. The first demo will showcase precise defect and contamination detection on the surface of a structured wafer. The second demo will highlight how MVTec's own deep-learning-based anomaly detection technology can be used to reliably detect defects on printed circuit boards. MVTec experts will be on hand to discuss these applications and provide detailed explanations on how machine vision can be utilized effectively.
About MVTec Software GmbH
MVTec is a leading manufacturer of standard software for machine vision. MVTec products are used in a wide range of industries, such as semiconductor and electronics manufacturing, battery production, agriculture and food, as well as logistics. They enable applications like surface inspection, optical quality control, robot guidance, identification, measurement, classification, and more. By providing modern technologies such as 3D vision, deep learning, and embedded vision, software by MVTec also enables new automation solutions for the Industrial Internet of Things aka Industry 4.0. With locations in Germany, the USA, France, China, and Taiwan, as well as an established network of international distributors, MVTec is represented in more than 35 countries worldwide. www.mvtec.com
Featured Product
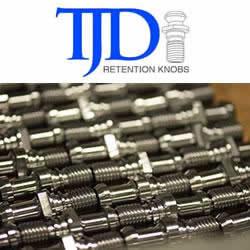