3E EOS Expands Additive Manufacturing Capabilities with Stratasys Technology to Reduce Lead Times and Lower Costs
New investment includes multiple F3300 printers, enhancing capabilities across the manufacturing lifecycle from prototyping to tooling and production for the aerospace, defense and automotive sectors
3E EOS, a leader in electro-optic systems, has expanded its additive manufacturing capabilities with a significant investment in Stratasys (NASDAQ: SSYS) technology, the company announced today. This expansion includes the addition of multiple Stratasys FDM 3D printers, bringing their total fleet to 15 large-scale systems, including the F3300, Neo800, F900, F770, Origin One models and SAF technologies.
Building on its existing success with Stratasys solutions, 3E EOS is establishing a dedicated additive manufacturing center to support prototyping, tooling and production. The expanded fleet enables the company to produce critical components such as air ducts and fuel adapters for aircraft, reducing lead times by 30-45 days compared to traditional manufacturing methods, and cutting production costs by 40 percent.
The Stratasys F3300 flagship printer continues to deliver tangible value for customers, driving its increased adoption in support of critical applications across the aerospace, defense, and automotive sectors. For example, with this solution, 3E EOS anticipates lowering costs for high-volume projects by 20 percent.
"In a world where trends evolve rapidly, staying ahead of the market is not just an advantage—it's a necessity," said Emir Ozdemir, Head of Market Development at 3E EOS. "Our continued partnership with Stratasys ensures we remain at the forefront of innovation, delivering cutting-edge solutions that exceed market demands. By equipping our team with the industry's best additive manufacturing technology, we empower innovation and drive excellence."
This investment underscores 3E EOS's commitment to adopting advanced technologies that deliver exceptional value. Stratasys' extensive material range and advanced 3D printing systems have allowed 3E EOS to streamline production workflows and meet customer needs with precision and efficiency.
Andreas Langfeld, President of EMEA and APAC at Stratasys, remarked, "3E EOS is demonstrating a forward-thinking approach by strategically adopting additive manufacturing for applications where it offers clear advantages over traditional methods. By developing impactful use cases and integrating AM into their operations, they've recognized its potential to drive efficiency and innovation. Their decision to establish a large AM center further elevates the value of additive manufacturing, enabling them to maximize its impact across the manufacturing lifecycle."
CoreLayer, alongside 3E EOS, is also concentrating on the evolving needs of the automotive industry, bringing its expertise in designing and manufacturing assembly line jigs and fixtures to this dynamic sector. By applying its proven capabilities, CoreLayer aims to support clients in adapting to increasingly complex designs and improving production efficiency. This strategic focus reinforces their role as a trusted partner for advanced manufacturing capabilities.
In addition, 3E EOS is advancing the adoption of additive manufacturing while promoting sustainability by minimizing material waste and energy consumption. This aligns with global environmental standards and supports their goal of fostering a more resource-efficient manufacturing process.
About Stratasys
Stratasys is leading the global shift to additive manufacturing with innovative 3D printing solutions for industries such as aerospace, automotive, consumer products, and healthcare. Through smart and connected 3D printers, polymer materials, a software ecosystem, and parts on demand, Stratasys solutions deliver competitive advantages at every stage in the product value chain. The world's leading organizations turn to Stratasys to transform product design, bring agility to manufacturing and supply chains, and improve patient care.
To learn more about Stratasys, visit www.stratasys.com, the Stratasys blog, X/Twitter, LinkedIn, or Facebook. Stratasys reserves the right to utilize any of the foregoing social media platforms, including Stratasys' websites, to share material, non-public information pursuant to the SEC's Regulation FD. To the extent necessary and mandated by applicable law, Stratasys will also include such information in its public disclosure filings.
Featured Product
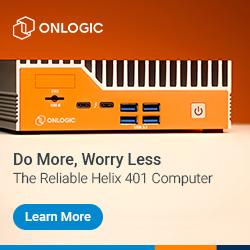