ACCUMOLD TO HIGHLIGHT MICRO MOLDING INNOVATIONS AT MD&M WEST 2025
Attendees visiting Booth 2844 will have the chance to see firsthand how Accumold enables medical device manufacturers to push the boundaries of innovation with incredibly small, precise components.
(21st January 2025, Ankeny, Iowa, USA) Accumold, a global leader in micro injection molding, is set to showcase its expertise at MD&M West in Anaheim, CA, from February 4-6, 2025. Attendees visiting Booth 2844 will have the chance to see firsthand how Accumold enables medical device manufacturers to push the boundaries of innovation with incredibly small, precise components.
"MD&M West is one of the largest events Accumold participates in each year, and we're always eager to showcase how micro molding is driving innovation in medical equipment and wearable devices. Our comprehensive capabilities have established us as a global leader in micro molding. With in-house tooling, quality assurance, and production all integrated under one roof, we're equipped to scale rapidly and sustain high production volumes — qualities that make Accumold the perfect partner for OEMs seeking a reliable micro mold provider. We look forward to connecting with everyone in Anaheim at Booth 2844!" says Brett Saddoris, Technical Sales Manager at Accumold.
Accumold has been at the forefront of micro molding for over three decades, working with medical OEMs to create parts that meet exacting tolerances, often down to a few microns. The company's capabilities include insert molding, two-shot molding, and cleanroom molding using materials such as PEEK and LCP. Its vertically integrated approach streamlines every stage of product development — from design support and tooling to metrology and automated assembly — delivering optimized outcomes in cost, accuracy, and time to market.
In the medical field, precision and reliability are paramount. Devices often serve critical applications where failure isn't an option. Accumold's ISO 13485 accreditation ensures that stringent quality standards are met, giving OEMs confidence in the consistency and scalability of their production runs.
Saddoris concludes, "What sets Accumold apart is its collaborative approach. The company partners with medical innovators to transform ambitious product concepts into reality, leveraging its unique expertise in micro manufacturing to achieve what others might consider impossible. Whether it's producing tiny fiber optic components or intricate wearable device parts, Accumold combines precision with scalability — from prototype to full production runs."
MD&M West attendees are invited to stop by Booth 2844 to explore examples of Accumold's work and discuss how the company's micro molding capabilities can help bring new medical devices to market faster and more efficiently.
Featured Product
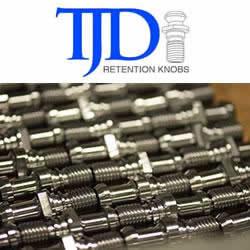