Boeing turns to 3D-printed parts to save millions on its 787 Dreamliner
Lucas Mearian for ComputerWorld: Boeing will begin using at least four 3D-printed titanium parts to construct its 787 Dreamliner aircraft and may some day rely on as many as 1,000 parts created via additive manufacturing.
Boeing has hired Oslo, Norway-based Norsk Titanium AS to print the parts. It marks the first time that FAA-approved, 3D-printed titanium parts will be used as structural components on a commercial aircraft, according to the company.
The parts will be used near the rear of the Dreamliner, a mid-sized, wide-body, twin-engine jet airliner. Boeing builds about 144 Dreamliners each year. Full Article:
Comments (0)
This post does not have any comments. Be the first to leave a comment below.
Featured Product
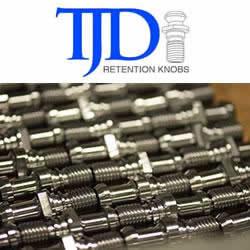