Renishaw showcases AM capabilities at RAPID + TCT
To share its expertise in medical device manufacturing, global engineering technologies company Renishaw is returning to RAPID + TCT, the leading additive manufacturing (AM) and 3D printing event in the United States. From the 21st to the 23rd of May 2019, Renishaw can be found on Booth 827 at the Cobo Center in Detroit, Michigan.
On Tuesday 21st May, at 3.30pm (EDT), Marc Saunders, Director of AM Applications at Renishaw and Alexis Dang MD, Chief Medical Officer at PrinterPrezz Inc. will give a talk explaining the clinical and manufacturing considerations when additively manufacturing spinal implants, as part of the AM Technical Insights Forum. The talk will explore the growing capabilities of additive manufacturing technologies and how they can be used in the medical sector to improve productivity when manufacturing customisable implants.
The talk will complement the exhibition of Renishaw's latest AM system, the RenAM 500Q, which includes four 500 W lasers in the most commonly used platform size. By speeding up the AM build process, manufacturers will see a drastic increase in productivity, leading to a reduction in cost-per-part, an increase in return on investment and a reduction in process waste. This will allow AM to be used in applications that were previously uneconomical.
At the show, Renishaw will also demonstrate its QuantAM build preparation software, developed specifically for use with Renishaw additive manufacturing systems. The dedicated software tool has an intuitive workflow and easy navigation to allow users to rapidly prepare models for the AM process.
“Additive manufacturing enables the design and manufacture of more complex medical devices,” explained Saunders. “By reducing design constraints, clinicians and medical device manufacturers can dedicate their time to catering for more complex conditions, match devices to an individual's anatomy and, in many cases, promote osseointegration.
Dr. Alexis Dang added, “Our presentation will explore the clinical benefits of spinal implants that have been designed with the patient in mind. When clinicians and engineers collaborate to utilize advanced AM technologies, designs are optimized for improved patient fit and enhanced osseointegration, for additive manufacturing and optimal post-processing. Our aim is to bring more advanced medical devices to market more quickly.”
“Using software specifically designed for Renishaw AM platforms allows users to unlock all the benefits of additive manufacturing,” continued Saunders. “Manufacturers can use QuantAM software for tighter integration into the machine control software and to accurately and rapidly review all build files for Renishaw AM systems.”
Saunders has over 25 years' experience in high tech manufacturing. At Renishaw, Saunders manages a global network of Solutions Centres for metal additive manufacturing, enabling customers who are considering deploying AM as a production process to gain hands-on experience with the technology before committing to a new facility.
Dr. Alexis Dang is a board-certified orthopaedic sports surgeon. He is an HS Clinical Associate Professor at UCSF. Along with his brother, Dr. Alan Dang, he started the Orthopaedic Rapid Intelligent Fabrication (ORIF) program at UCSF/San Francisco VA and is a founding member of the UCSF Center for Applied 3D+ Technologies. Dr. Dang is also Chief Medical Officer at PrinterPrezz, Inc., a trailblazer in combining metal 3D printing, nanotechnologies, and surgical expertise to design and manufacture next generation medical devices.
For more information about Renishaw's additive manufacturing software and systems, visit www.renishaw.com/additive
Comments (0)
This post does not have any comments. Be the first to leave a comment below.
Featured Product
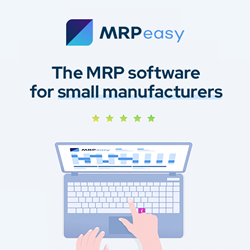