Time to fight corrosion – for the environment’s sake
The global cost of corrosion exceeds US$2.5 trillion annually, or three percent of global GDP. Moreover, the environmental consequences are enormous. Innovative premium high-strength and high-performance stainless steel fasteners offer significant benefits – from product and asset infrastructure maintenance to total lifecycle costs – in many global industry sectors.
By Nimeka de Silva and Patrik Lundström Törnquist
Metallic corrosion is the result of electro-chemical interaction between a metal and substances present within its operating environment. Corrosion results in degradation of that material, to the point where it is no longer mechanically or structurally fit for purpose. Corrosion presents a formidable global challenge. It affects many everyday products and almost all infrastructure – through increased maintenance, shorter product lifecycles, end-of-life management and generally the overall utilization of more resources over a product’s lifetime.
The economic and environmental impact is significant, and it is high time to place the fight against corrosion in a proper sustainability context.
The International Measures of Prevention, Application and Economics of Corrosion Technology (IMPACT) study by NACE estimates the global cost of corrosion to be US$ 2.5 trillion annually – equivalent to around three per cent of global GDP in 2018. However, it also estimates that existing corrosion control practices could save 15-35 percent of the cost of corrosion, equating to between US$ 375 and US$ 875 billion globally each year (NACE International, 2016).
Corrosion impacts heavily on the environment
The consequences of corrosion-related impacts on the environment are not included in this study but are increasingly important. In response to greater interest in issues related to environmental impact and sustainability, engineers are ever more encouraged to design products and infrastructure that can minimize negative environmental and societal impact. Sustainability in design, optimizing a product’s lifecycle, minimizing maintenance requirements and end-of-life upcycling/recycling for example are all becoming an important part of product performance, quality and overall cost.
In future, it is very likely that we will see even more burden placed on product manufacturers and asset infrastructure owners towards end-of-life management, so making early considerations in the design and planning stage will become a more crucial aspect of engineering. Life Cycle Assessments (LCAs) are becoming ever more important for any product or project from both a customer and regulator perspective.
More robust and cost-effective fastener solutions
Stainless steel fasteners have long been used in corrosive environments, such as within the oil & gas industry, chemical processing, marine and coastal applications. In recent years, stainless steel materials, predominantly austenitic grades A2 (304) and A4 (316), have become more readily available, largely due to low-cost high-volume Asian manufacturers.
However, interest in premium stainless steel and high-grade alloy fasteners has really taken off. Within the correct application, they offer improved product performance, reduced maintenance and can help to maximize the product lifecycle. Considering total lifecycle costs can help to deliver significant cost efficiencies over the lifespan of a product, rather than an approach focusing purely on the initial upfront cost.
Particularly in more technical industries where performance, safety and reliability are all critical factors, engineers are now starting to give more consideration to an ever-increasing range of fastener products and material options available to them, in an attempt to design more robust and long-term cost-effective products and infrastructure.
Traditional fastener challenges for engineers
One of the traditional limitations accepted by engineers when considering the use of stainless steel materials, is reduced mechanical strength compared with high tensile carbon steel. If a combination of high strength and corrosion resistance was required, then engineers may often resort to the use of high tensile carbon steel with an additional protective coating.
However, high tensile carbon steel brings with it the burden of finding a coating suitable for the application and the associated performance, quality and lifespan considerations for the coating. High tensile carbon steels are also prone to the risk of hydrogen embrittlement as a result of their manufacturing process. Engineers often express concerns regarding this risk and careful consideration should always be given during their production.
The solution – corrosion resistance and high strength
Enter premium high corrosion-resistance stainless steel fasteners. These are products that combine the corrosion resistance capabilities of different stainless steel material grades, with the strength of high tensile carbon steel (such as the BUMAX DX 129 range). In addition, ductility and fatigue properties are also considerably better, outperforming high tensile carbon steel. By eliminating the limitations of strength in stainless steel materials, these premium fasteners open up new possibilities for design engineers that require a combination of high mechanical performance and corrosion resistance.
Applications for these premium stainless steel fasteners include aerospace, offshore equipment, steel construction, high-end electric bikes, high pressure applications, fueling systems and semiconductor manufacturing equipment – all with excellent results. Many more applications may follow, to the benefit of not only the owners and users of products and infrastructure – with higher quality, reduced maintenance and longer lifespans – but also the entire planet with the potential for the more sustainable use of material resources.
Nimeka de Silva is Development Manager, UK & Ireland, for BUMAX, a leading Swedish specialist manufacturer of premium stainless steel fasteners. A chartered mechanical engineer with an MBA from Aston Business School, Nimeka has experience in engineering, project management and commercial roles across the construction, energy and manufacturing industries. See www.bumax-fasteners.com
Patrik Lundström Törnquist is Managing Director of BUMAX. He has more than 20 years of experience from C-level positions in the global mining, steel, manufacturing and engineering industries. He has an M.Sc. from the Chalmers University of Technology and an M.B.A. from the Hult International Business School.
Comments (0)
This post does not have any comments. Be the first to leave a comment below.
Featured Product
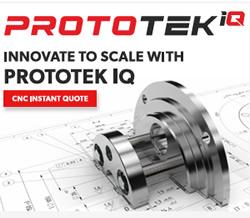