Vapour Degreasing – The Answer to Cleaner Components
The perfect finish is crucial when it comes to producing quality components. Achieving the correct surface is fundamental to further processes like coating, adhesion, plating or simply to improve the final appearance. One way to produce a good quality finish is through critical cleaning parts with vapour degreasing.
When it comes to critical cleaning parts, finding a long-term process that works effectively and adapts to changing requirements is the ideal. Even the smallest amount of surface contaminant whether it’s oil, grease, adhesives, fingerprints or other particulate, can impair a finishing method and result in parts not functioning reliably.
Critical cleaning is becoming more of a challenge due to the increasing use of miniaturised parts and complex geometries. Smaller components have tighter tolerances, which brings increased complications when manufacturing and finishing. To perform as they should, intricate components must be precision cleaned. This, however, can be a difficult process to navigate when adding in factors like hard to clean residue, cost implications or the ever-changing environmental restrictions and workplace safety rules being placed on companies today.
How Vapour Degreasing Works
A method that is re-gaining acceptance as a comprehensive and effective cleaning process is vapour degreasing. Vapour degreasers are a closed-loop system that require two elements: a specially designed cleaning machine, and a specific low-boiling, non-flammable fluid as the cleaning agent. Vapour degreasers contain two chambers: the boil sump and the rinse sump. In the boil sump, the solvent is heated, and the parts are immersed and cleaned in the fluid. Once cleaned, the parts are mechanically transferred to the rinse sump for final rinse in a pure, uncontaminated fluid. The parts come out clean, dry, spot-free and immediately ready for the next step in the process or packaging.
The cleaning fluids used within the system have multiple chemical properties that are advantageous to critical cleaning. For example, they typically have a low surface tension and a very low viscosity, allowing them to easily penetrate and clean very tight spaces like blind holes and the crevices between stacked parts. Most vapour degreasing fluids also are very heavy and dense, typically 20-40% heavier than water, which aids in dislodging particulate from the components.
Improving Worker Safety
Importantly, using a vapour degreasing process is a good way to address worker safety, regulatory requirements and environmental concerns. Leading companies are developing and commercialising non-toxic, environmentally acceptable cleaning options that out-perform older cleaning fluids like nPB, Perc or TCE.
What makes modern vapour degreasing chemistries even more impressive is that they also have ‘green credentials’ with a low VOC formula, which is ozone-friendly and complies with many regulations including F-Gas, and REACH.
Conclusion
To achieve a high-quality surface for finishing, cleanliness is an essential step, and one that should be investigated thoroughly to ensure components are ready for the next stage of manufacture. Vapour degreasing offers one solution. By using modern, highly advanced cleaning fluids, the process is simple, consistent and sustainable, resulting in perfectly cleaned parts. In addition, its flexibility to adapt to any future changes, whether it’s regulatory, environmental or a change in cleaning requirements, makes vapour degreasing a highly useful cleaning process for the finishing world.
Venesia Hurtubise is a Technical Chemist at MicroCare Corporation, which offers precision cleaning solutions. She has been in the industry more than 6 years and holds a MS in Green Chemistry from Imperial College. Hurtubise researches, develops and tests cleaning-related products that are used on a daily basis in precision cleaning and medical applications. For more information, visit www.microcare.com.
Photo Captions:
- Industrial Products: Parts cleanliness is fundamental to further processes like coating or plating.
- Vapour Degreaser Overview: Vapour degreasing re-gaining acceptance as a comprehensive and effective cleaning process.
- Tergo MCF Composite image: Non-toxic, environmentally acceptable cleaning options are available for vapour degreasing.
Comments (0)
This post does not have any comments. Be the first to leave a comment below.
Featured Product
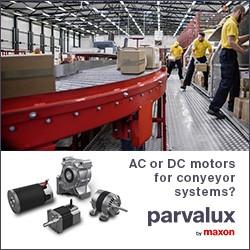