World’s first 3D printed FRP footbridge paves way for circular composites
The world’s first lightweight 3D printed fiber reinforced polymer (FRP) footbridge will be installed at Kralingse Bos park – the green heart of Rotterdam. This heralds the transition towards the next generation of bridges, offering high performance with extreme versatility, circularity and sustainability.
.jpg)
Royal HaskoningDHV, DSM - a global purpose-led, science-based company in Nutrition, Health and Sustainable Living, and City of Rotterdam, have announced the intention to collaborate in the design and build of a new circular composite footbridge which will be installed in Rotterdam.
Rotterdam is a dynamic, innovative city at the forefront in the use of composite bridges to underpin the city’s drive towards circularity and sustainability.
Sustainability and the next generation infrastructure
Mozafar Said, Asset Manager from the City of Rotterdam, said: “The city of Rotterdam is proud to be a leader in the smart and circular use of composite bridges. Together with Royal HaskoningDHV and DSM, we are continuing to push the frontiers of sustainability for bridges, using thermoplastics which will enable greater circularity.
“The 3D-printed FRP footbridge as a circular composite aligns with our city’s ambitious sustainability targets to reduce carbon footprint and promote liveability and we are proud to be the first city to test, print and install it.
“We see the use of composite bridges as a smart solution to replacing our older constructions. With more than 1000 bridges in Rotterdam, we are constantly looking to push the boundaries to develop the next generation of bridges which will be more sustainable and circular with lower maintenance and lifecycle costs.”
Circular composites
According to Maurice Kardas, Business Development Manager at Royal HaskoningDHV: “We announced the prototype of this circular composite bridge in 2019 and with the vision and support of our partners DSM and the City of Rotterdam we can now take this one step further.
“Rotterdam and the Netherlands are ahead of the curve in innovation in infrastructure, particularly in the areas of sustainability and circularity. By introducing circular composites into their bridge infrastructure, Rotterdam proves once again to be a city ahead of the game. This is a step change which signifies a collective effort to bring innovation from idea to realization and ushers in a new era of sustainable design and bridge functionality.”
The circular composite footbridge is made from a fiber reinforced thermoplastic called Arnite® which combines high performance with circularity.
Patrick Duis, Senior Application Development Specialist Additive Manufacturing at DSM added: “The printed circular composite bridge enables the transition to a more sustainable and circular type of bridges with minimal wear and tear. Now that we have the new circular composite of recyclable source material along with the required performance properties available to us, we can start taking the environment-friendly design of the infrastructure to the next level.”
A modern, durable footbridge solution
The footbridge will be developed strictly in line with the highest standards of safety for FRP bridge design. The city of Rotterdam infrastructure experts in composite bridges will be closely involved in the design and build process.
Sensors could also be included into the footbridge to build a digital twin of the bridge. The sensors can predict and optimise maintenance, ensuring safety and extend the life span of the bridge. It is estimated the footbridge will be installed and in use by the end of 2020.
Comments (0)
This post does not have any comments. Be the first to leave a comment below.
Featured Product
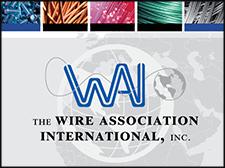