The Role of RO in Industrial Manufacturing
When most people hear “reverse osmosis” (RO), their minds likely go to drinking water. While purifying drinking water is a significant use case for it, and arguably its most notable, RO has far broader applications. Many industrial manufacturers rely on reverse osmosis for various processes.
RO reverses water’s flow to pass it from a more concentrated solution through a semi-permeable membrane to a less concentrated one. These membranes contain pores roughly 0.0001 microns in diameter, removing most contaminants. This, along with the pre and post-filters which often appear in these systems, makes RO a remarkably effective filtration method.
Here’s how this process helps in industrial manufacturing.
Ensuring Product Safety and Quality
Products that contain water often need to ensure that it’s of the highest quality. Products that contain unclean water could fail to meet quality standards at best and endanger users at worst. Passing this water through RO systems first removes harmful or poor-tasting contaminants, preventing these situations.
Industrial RO systems typically feature between three and five filters, ensuring no contaminants get through. These filters have increasingly small pore sizes, removing smaller and smaller particles until the water is pure. The resulting water is so clean that it’s safe enough for even medical applications like vaccines.
Pharmaceuticals is the most obvious use case for this process, but it’s helpful in other manufacturing sectors, too. Food production, for example, requires clean water to make beverages safe for consumption. If a manufacturer uses water for washing their products, they’ll need to ensure it’s free of contaminants as well.
Minimizing Waste
Another way that industrial manufacturers use RO is to minimize their water waste. Growing populations, climate change and irresponsible consumption have made clean water increasingly inaccessible in many areas. Some experts say this could create a water shortage as soon as 2040, so minimizing water waste is essential.
To help fight water scarcity, manufacturers can collect their runoff and other wastewater. Passing it through a reverse osmosis system will clean it enough to use in future processes. This capturing and filtering method creates a kind of circular water economy that can drastically reduce manufacturers’ water waste.
As an added benefit, minimizing waste in this way also saves manufacturers money. While installing an RO system may be expensive upfront, reusing water will make up for those costs over time. These financial benefits of RO can help convince manufacturers to adopt more sustainable business practices.
Cleaning
Industrial manufacturing facilities can also use RO in the equipment cleaning process. While easily overlooked, cleaning is an essential part of machine maintenance, especially with more delicate or expensive equipment. Failure to keep these machines clean can result in buildup that hinders their performance, even to the point of breaking down.
RO helps in this area because many water systems deliver hard water, which can be counter-productive in cleaning. Hard water contains high levels of minerals like calcium and magnesium. These minerals can react with soaps, leaving residue that requires extra cleaning.
Since reverse osmosis moves water through such minuscule pores, it removes these microscopic impurities. By treating their water with RO before cleaning, manufacturers ensure that they can clean their equipment effectively. They won’t leave any residue behind and will save on cleaning materials costs.
RO Is Crucial in Many Manufacturing Settings
Reverse osmosis may not seem like a crucial part of manufacturing to some people at first. Despite these assumptions, many manufacturers rely on it, whether it’s to ensure product quality, minimize waste or clean equipment. Many of these processes would be far more expensive, ineffective or inconvenient without RO.
The leading industrial manufacturers need everything to meet rigorous quality standards. RO ensures that even the water they use is top-quality.
Comments (0)
This post does not have any comments. Be the first to leave a comment below.
Featured Product
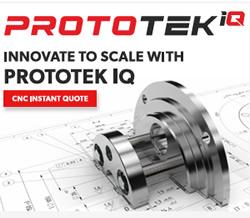