5 Promising Innovations in Metal Finishing Techniques
Metal finishing is a crucial process in many modern manufacturing operations. While the practice itself is by no means new, the industry has likely only scratched the surface of its potential. Demand for faster, cheaper and more resilient finishing is rising, driving innovation.
The metal finishing market was worth $95.2 billion in 2020, and experts predict strong future growth. As manufacturing itself grows, producers will have more need for various metal finishing processes. Consequently, advances in the latter have positive ripple effects on the former.
A Review of the Metal Finishing Process
Metal finishing often falls towards the end of the manufacturing process. While the specifics vary between facilities, technologies and goals, it generally entails coating, cleaning or otherwise treating metal to improve its performance or aesthetics. Some finishes make metal 85% more resistant to corrosion, while others may simply make it more attractive.
Metal finishing covers multiple different processes, but some of the most common include:
- Electroplating
- Brushing
- Polishing
- Grinding
- Blasting
- Powder Coating
- Vibratory finishing
- Heat-treating
- Hot blackening
Brushing, polishing, and grinding are among the simplest forms, involving smoothing metal surfaces with abrasive materials instead of treating them. Blasting and vibratory finishing achieve a similar effect but use more advanced methods to achieve it.
Heat-treating and hot blackening both use high temperatures to make metals more durable. Hot blackening deposits a layer of black oxide to improve abrasion resistance, and heat-treating hardens the metal.
Electroplating and powder coating are the most advanced forms and are likely what comes to mind when people think of metal finishing. Electroplating uses chemicals and an electric current to adhere a thin layer of metal over the product. Powder coating, by contrast, uses UV or heat curing to form a layer of plastic powder over the surface.
Recent Innovations in Metal Finishing
Many of these metal finishing techniques have been around for decades, some even longer. Despite basic finishing concepts being rather old, metal finishing today often looks nothing like it once did. In the past few years, many groundbreaking innovations have pushed the practice further.
These advancements are making metal finishing more effective, affordable and sustainable. As consumers and corporations alike demand more from their parts and materials, these practices become increasingly valuable. Here’s a look at five of the most disruptive innovations in metal finishing.
1. Hydrophobic and Hydrophilic Prepainted Metal
Prepainted or coil-coated metal involves applying even paint layers before fabrication, ensuring a more even and durable finish. The practice itself has been in use since the mid-20th century, but new technologies have made it more valuable. Some of the most promising of these are hydrophobic and hydrophilic coatings.
Hydrophobic prepainted metal repels water, causing it to bead and roll off easily. This property also makes it difficult for other materials to stick to the surface, enabling quick, easy cleaning. Considering how cleaning graffiti costs $12 billion annually, metals with these coatings can lead to substantial savings for companies and public services.
By contrast, hydrophilic coil coating attracts and retains water, which reduces friction. These coatings have become popular for medical devices as they minimize the risk of tissue damage through improved lubrication. They can also protect against corrosion in water pipes by reducing friction with abrasives like salt or other minerals.
2. Nanotech Coating
While nearly all modern metal finishes are extremely thin, new technologies have enabled nano-scale coatings. These finishes are between 1 and 100 nanometers thick, while a human hair is 80,000 to 100,000 nanometers wide. This microscopic scale gives manufacturers more control over metal’s properties and can provide desirable qualities with minimal mass increases.
One of the most valuable applications of nanotech coatings is improving durability. Repairing a scratched car can cost as much as $3,500, and traditional scratch-resistant finishes may affect paint color or material thickness. Nano-coatings can make car surfaces resistant to abrasion without compromising their other qualities, thanks to their thinness.
Other nanotech coatings can make metals hydrophobic or hydrophilic, improve electrical conductivity or even make them anti-microbial. As nanoscience advances, the possibilities will expand further.
3. Green Electroplating
Electroplating has many benefits, but traditional methods are far from environmentally friendly. The use of toxic solvents runs the risk of leaking dangerous chemicals into the environment, and the process is often energy-intensive. Recent innovations are making it a more sustainable practice.
One such method dissolves aluminum in water instead of solvents. Aluminum is less harmful to the environment than typical materials like chrome and cadmium, and using water removes the risk of dangerous chemical leaks. This process also doesn’t require highly specialized, energy-hungry machinery, reducing greenhouse gas emissions.
Some modern electroplating processes avoid wet surface finishing entirely. This cuts potentially harmful solvents out of the equation and minimizes industrial waste. While dry electroplating hasn’t fully replaced wet processes yet, it’s a growing technique.
4. Graphene Plating
One rapidly growing metal finishing innovation isn’t a new process but a material: graphene. Graphene is a single layer of carbon atoms, making it the thinnest material known to humans, and has many remarkable properties. It’s 200 times stronger than steel, has excellent electrical and heat conductivity and is highly flexible.
Plating metals with various graphene-based materials can give many products and parts these properties. For example, graphene can make metals resistant to chemical, heat and moisture corrosion, ideal for vehicles or industrial applications. Similar properties can help make medical devices more durable and sanitary.
As the renewable energy market expands, graphene plating in solar cell production becomes more valuable. These platings could be the key to making more efficient, flexible solar panels for more varied applications.
5. Data Analytics
Like many industrial processes, metal finishing has also improved with the introduction of data analytics. Since this field covers so many different processes and techniques, there could be multiple solutions to the same problem. Data analytics can weigh these options to suggest workflow improvements for metal finishing operations.
For example, data from an electroplating process could show that its energy consumption is too high. Analytics engines could then suggest possible solutions, such as using different solvents or adjusting other parts of the workflow to use less power. The facility could then implement these changes and save both energy and money.
Data analytics enables metal finishing operations to embrace a strategy of ongoing improvements. As new technologies and techniques emerge, they’ll have more options for these adjustments. Metal finishing as a whole will become a more optimized field.
Finishing Innovations Promise Substantial Improvements
Few metal products reach their final form without some type of finishing. These innovations ensure that manufacturers can provide the best metal products possible and achieve them with minimal costs.
As more facilities implement these technologies and techniques, metal finishing will advance further. New possibilities will emerge, leading to better products and more optimized processes.
Comments (0)
This post does not have any comments. Be the first to leave a comment below.
Featured Product
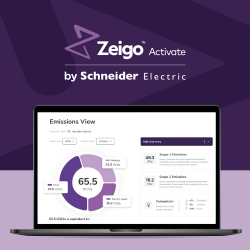