Metalworking Industry Sees Surge in Automation Adoption
While the basic steps in metalworking remain unchanged over the years, businesses increasingly rely on machines to complete them. While not unique to fabrication, this shift is seeing particular growth in the sector, so companies within the industry should pay attention.
Why Prefab Shops Should Digitize Their Workflows & 5 Entry Points
Widespread prefab construction adoption remains to be seen, but the positive impact these techniques can offer on project outcomes is well-known among construction technologists.
HORIZON LAUNCHES BREAKTHROUGH TECHNOLOGY AT FORMNEXT 2022
Horizon Microtechnologies commercially launched it ground-breaking template-based 3D-microfabrication technology, which produces conductive micro additive manufacturing (micro-AM) derived parts with micrometer scale precision.
5 Amazing Ways Automation Benefits Fabrication
Most sheet metal fabricators seek ways to improve productivity and become more efficient to stay competitive. Automation has evolved significantly in the past few years, and a growing number of solutions can provide significant value to companies.
How Will Labor Shortages Impact Metal Fabrication in 2022?
The American Welding Society estimates a 400,000-worker shortage by 2024. The urgent need for more welders and higher skill levels among welding personnel is widely known and accepted in the U.S. manufacturing industry.
Metal Fabrication Shop Utilizes Efficient Production Method
When a client needs a prototype created quickly, longer-running fabrication jobs most likely will have to be be put on hold to make room for a rapid prototype manufacturing job.
5 Promising Innovations in Metal Finishing Techniques
Metal finishing is a crucial process in many modern manufacturing operations. While the practice itself is by no means new, the industry has likely only scratched the surface of its potential.
Waterjet, Oxycut, Plasma or Laser, Which Cutting Technology Should I Use?
There is significant competition in the market between different cutting technologies, whether they are intended for sheet metal, tubes or profiles. There are those that use methods of mechanical cutting by abrasion and others that prefer thermal methods.
Ways Automation Is Changing Metal Fabrication
Growing demand and a widening industry skills gap have metal fabricators looking for ways to improve efficiency and product quality, even when additional labor may be hard to find.
ManufacturingTomorrow - Special Tradeshow Coverage
FABTECH EXPO Chicago
FABTECH EXPO takes place in Chicago, IL November 11th - 14th. This ManufacturingTomorrow.com Special Tradeshow report aims to bring you news, articles and products from this years event.
ManufacturingTomorrow - Special Tradeshow Coverage
FABTECH 2018
FABTECH takes place in Atlanta, GA November 6th - 8th. This ManufacturingTomorrow.com Special Tradeshow report aims to bring you news, articles and products from this years event.
Reducing Parts Costs as Production Scales Up
OEMs turn to one-stop metal parts shops that can transition to more cost-effective fabrication and machining techniques as demand increases.
Records 1 to 12 of 12
Featured Product
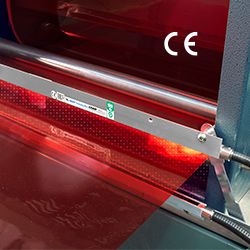
EXAIR's Chip Trapper
Chip Trapper offers a fast, easy way to clean, chips and shavings out of used coolants/liquids. The Chip Trapper can fill or empty a 55-gallon drum in less than two minutes. All the chips and other solids are trapped inside the reusable filter bag. https://exair.co/184_5171
EXAIR is offering a special right now on all of their Industrial House Keeping Vacuums. Learn more at https://exair.co/184-ihppromo