Rethinking material usage - How 3D printing enables dematerialization
According to a report from TAPP Water, worldwide bottled water consumption continues to grow. In 2018, we consumed over 100 billion gallons globally — that’s one million bottles per minute. As most of the environmental impact from bottled water comes from the packaging, drinking tap water, if safe to do so, is a more sustainable option. Global supply chains also have a large carbon footprint — we must identify more sustainable methods of making and transporting goods. Here Avi Reichental, chairman and co-founder at ultrafast polymer 3D printing pioneer Nexa3D, explores how manufacturers can reduce material usage without compromising on quality or productivity.
When calculating the carbon footprint of a product, we look at three key areas — materials, manufacturing processes and transportation. The embodied energy — everything that goes into a raw material, from extraction and purification to production and transportation — of the materials products are made from is an important, yet almost invisible, contributor to the total carbon footprint of a product.
Manufacturers regularly work with raw materials that have a large embodied energy, such as metals, because they are strong and durable. Traditional metal manufacturing methods require manufacturers to cut or machine parts from larger amounts of material, leading to wasted material that is unlikely to be used on other parts. 3D printing makes it possible to introduce different materials into production that offer a lower embodied energy. In many applications, polymer or composite materials can offer the same strength and durability as metals.
In a well-established process, overhauling both your material and production process can seem daunting, but the payoff to both the environment and your business could be enormous. Artificial intelligence (AI) powered software can help manufacturers to identify some low-hanging fruit, such as aftermarket parts, that could be redesigned for the new process as a starting point. Once you have established that the 3D printing production process meets your productivity and quality needs, engineers can then upscale its use into industrialized applications across the business.
Reducing material use
Rather than removing material, additive manufacturing (AM) builds the product layer by layer, significantly reducing material usage. Not only that, but additive manufacturing enables product developers to optimize their designs to improve part performance while minimizing material usage. For example, designers can consolidate parts to remove unnecessary joints that create weak points.
When producing a part using AM, it doesn’t matter how complicated or intricate the part needs to be. Designers can create internal details, lattices or other complex geometries that cannot be replicated using traditional manufacturing processes, creating a more lightweight and energy-efficient part. The result? A lower embodied energy, reduced transportation costs and a smaller carbon footprint.
Just as drinking tap water prevents the need for heavy bottled water to be transported to site, 3D printing means we can produce parts with better material use and reduced freight costs and emissions. In fact, a recent paper from researchers at Delft University of Technology predicts that additive manufacturing could reduce global energy usage by 25 per cent by 2050. However, to achieve this 25 per cent reduction, we need drastic and rapid change. Manufacturers must stop clinging to traditional processes and digitalise their supply chains sustainably, for the sake of our planet.
To find out more about Nexa3D, its product range and how you can start your sustainability journey, visit https://nexa3d.com, like us on Facebook, or follow us on Instagram, Twitter, and LinkedIn.
About Nexa3D
Nexa3D is passionate about digitizing supply chain sustainably. The company makes ultrafast polymer 3D printers, that deliver 20X productivity advantage, affordable for professionals and businesses of all sizes. The company partners with world-class material suppliers to unlock the full potential of additively manufactured polymers for volume production. The company makes automated software tools that optimize the entire production cycle using process interplay algorithms that ensure part performance and production consistency, while reducing waste, energy, and carbon footprints. For more information, please visit www.nexa3d.com.
Comments (0)
This post does not have any comments. Be the first to leave a comment below.
Featured Product
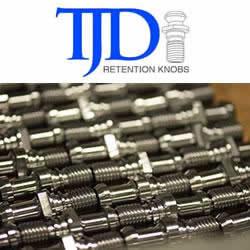