Copper Shortages Present New Manufacturing Challenges in 2022
Supply shifts are a continually present challenge for manufacturers. In the past few years, shortages and delays have become increasingly prevalent, causing more widespread disruptions across manufacturing. One of the latest and most impactful of these shortages is copper.
While the refined copper market had a 142,000-ton surplus in 2020, experts predict that to fall to a 219,000-ton deficit by 2025. This shortage has already started to take effect and will have increasingly severe consequences as it continues.
Where the Copper Shortage Comes From
Like many many supply issues, the current copper shortage is multifaceted. It began with skyrocketing demand, largely from the COVID-19 pandemic and sustainability initiatives.
Copper has inherent antimicrobial properties, making it an ideal material for high-touch surfaces amid a viral outbreak. The pandemic also drove copper demand as consumers spent more time indoors, buying more electronics to help pass the time. As an excellent conductor, copper is a key component of many electronic devices.
Sustainable technologies like solar panels and electric cars also rely on copper components. As people have grown more concerned about the environment, demand for these products has surged. Demand for copper naturally grew alongside it.
As these trends took hold, copper production failed to keep pace. Only two major copper mines have opened in the last four years, and regulatory restrictions have inhibited existing mines’ growth. When COVID-19 struck, many facilities also had to pause or reduce operations, causing the industry to quickly fall behind demand.
Challenges of Copper Shortages in Manufacturing
Many of the world’s major copper mines have since resumed normal operations. However, their temporary pauses amid surging demand were enough to place them far behind. As demand continues to climb, the shortage will likely continue for some time.
Here’s how this shortage could challenge the manufacturing industry this year and beyond.
Rising Material Prices
One of the first changes manufacturers will notice is a rise in material prices. Copper is a common component in products ranging from electronics to pipes. As demand continues to rise and supplies remain tight, prices will naturally rise, impacting manufacturers’ bottom lines.
This change has already begun, and it will likely grow more severe as the copper shortage continues. Prices soared to $4.53 per pound in mid-2021, their highest since February 2011. Experts warn that if these trends continue, copper could reach as much as $9.07 per pound.
Manufacturers face a difficult choice amid these rising material prices. They could either raise their prices to account for the change, possibly losing clientele, or they could accept a slimmer profit margin.
Production Shortfalls
Since demand shows no signs of slowing down, the shortage risks growing worse over the coming years. In some areas, manufacturers may not be able to get as much copper as they need, regardless of its price. With fewer raw materials, production will decline.
When manufacturers fall short of their production quotas, several other obstacles will emerge. They may face pressure from investors, possibly losing them if the shortfalls get too extreme. As their clients become unable to order their usual amount, they may look for business elsewhere.
Of course, lower production also results in less revenue flowing in, as there’s less to sell. This, combined with potentially lower profit margins from rising material costs, could deliver a substantial financial blow.
Clientele Loss
Rising prices and declining production levels will likely result in clientele loss for some manufacturers. While the copper shortage will affect every manufacturer that relies on the metal, some may still risk losing business to competitors. Some facilities may have to raise their prices more than others due to slimmer starting profit margins, leading to customer churn.
In 2020, 51% of U.S. consumers switched brands because another one offered lower prices. People are willing to forsake brand loyalty for a lower price, which will reflect even in B2B markets. If a B2B manufacturer supplies a B2C brand, changes in the B2C brand’s customer base will come back to affect the manufacturer.
How extreme this customer churn will be is still uncertain. While the copper shortage’s impacts will be uneven, it’s unclear how uneven they will be, so price hikes may not vary much between manufacturers. Still, the industry should prepare for this scenario to be safe.
Obstacles for Sustainable Manufacturing
Declining copper supplies will also present a challenge for manufacturers invested in sustainability. Many producers have committed to sustainable technologies, such as Maserati investing $867 million in electric vehicles, but these require copper.
Solar panels and wind turbines also use copper for its conductivity, but production on these may slow in the face of shortages. Alternatively, manufacturers producing these products may have to raise their prices, harming the shift to sustainability. Sustainable technologies must be affordable to replace traditional counterparts, which will be difficult with rising copper prices.
These price hikes and production shortages could drive people away from sustainable technologies. Manufacturers that rely on these products as their chief revenue drivers may face dropping demand.
Supply Chain Complications
Finally, the copper shortages could complicate manufacturers’ supply chains. As mines become unable to produce sufficient copper to meet demand, manufacturers may turn to distributed sourcing. While this can help mitigate shortages, it could be a complicated transition.
Manufacturers may have to source from mines farther away than their typical sources. This will incur higher transportation costs and could introduce more international shipping complications. Manufacturers may also have to restructure their schedules to account for shipments taking longer to reach them.
Potential Mitigation Strategies
While these challenges are substantial, copper shortages don’t spell the end for manufacturers. Businesses may not be able to avoid these obstacles, but they can prepare for and mitigate them.
Recycling may be the best way forward for manufacturers. Organizations can recycle copper repeatedly without any performance loss, opening the door to a circular copper economy. If manufacturers switch to using recycled copper instead of new metal, they could decrease their reliance on declining mines.
This transition will cause some initial disruption and expenses, but it will eventually provide the most cost-effective way forward. In the meantime, manufacturers may have to account for rising prices. Companies should evaluate their specific markets to determine if rising end-product prices or accepting a slimmer profit margin is the safest strategy.
Increasing communication and transparency between supply chain partners is also crucial. Manufacturers should stay in constant contact with copper suppliers and logistics providers to anticipate any incoming shortages, delays, or other disruptions. If they can react faster, they can mitigate these obstacles’ severity.
The Manufacturing Sector Must Brace for Disruption
Copper is an essential resource for manufacturers across various sectors. While the current shortages may not last forever, the industry must heed the warning signs and brace for change.
If manufacturers continue to operate without any adjustment, the copper shortages could have substantial consequences. However, if they can anticipate these obstacles and react accordingly, they can emerge relatively unscathed.
Comments (0)
This post does not have any comments. Be the first to leave a comment below.
Featured Product
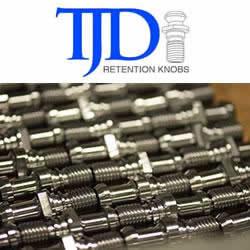