Optimize Sales With a Reorder Point Formula
A reorder point formula can be an invaluable tool for effective inventory management. At the right level, the reorder point will ensure that a business automatically reorders essential raw materials, components and products. Doing so guarantees their availability if possible.
However, a reorder point can cause storage utilization issues and wasteful spending when set too high. When it’s too low, the reorder point may not prevent stock-outs or shortages of key materials.
By using a reorder point formula, manufacturers can ensure that their reorder points are set to optimal levels, providing effective reordering and helping streamline inventory management.
What Is a Reorder Point?
The reorder point is the inventory level at which an order triggers to refill stock above a certain level. Higher reorder points help ensure that inventory is always available, while lower ones help reduce item reorder frequency.
For example, once a manufacturer’s store of copper dips below the ROP, an inventory management or logistics solution can automatically order additional copper from a supplier, guaranteeing future availability of the material. The point can help businesses ensure that vital products and materials are always available.
Generally, each item or SKU in a business’s storage will have a reorder point. Manufacturers may want an ROP for each raw material, component or product they need for daily operations.
Determining the right ROP can be challenging — especially if a manufacturer’s consumption of a particular inventory item can vary significantly. Uncertainty means future inventory levels may be difficult to predict.
Building a Reorder Point Formula
An ROP formula helps businesses automatically determine the optimal ROP for each SKU or item they need to keep stocked. Most ROP formulas use several kinds of input data to determine the ROP, including:
- Maximum, minimum and average daily usage of an item
- Maximum, minimum and average lead time for new orders of an item
- The level of safety stock for that item
For example, here is one of the simplest and most common ROP formulas:
- ROP = (average daily usage in units x average lead time in days) + safety stock in units
This formula will ensure that if the average usage of an item rises high enough that waiting for an order will deplete the business’s safety stock, the ROP will trigger a new order.
The formula above assumes consumption is more or less consistent, which may not be accurate for every item.
A “safer” version of this formula would replace average usage and lead time with maximum usage and lead time. This formula would likely produce a higher reorder point but would also ensure that fluctuations in use would be less likely to deplete the business’s safety stock.
What Makes for a Good ROP and ROP Formula?
The ideal ROP is dynamic and businesses should recalculate them at regular intervals — possibly every three to six months. Assessing the ROP more frequently will help ensure the reorder point reflects current trends in item usage and supplier lead times.
When recalculating the ROP, it’s a good idea to use inventory data from the period between now and the last time a company calculated it. This inventory data can show managers if the current ROP was effective, too low or too high.
Certain businesses may also need to recalculate their ROP or revise their formula more often. Supplier changes, bill of materials changes and rapid business growth may all render existing ROP formulas obsolete, requiring the business to generate a new ROP or procedure.
Strong supplier relationships are essential to inventory management and can significantly impact item prices or lead times. Businesses that damage their relationship with a critical supplier or have to change suppliers may need to increase their ROP to compensate for increased lead times.
Coordination with suppliers may also provide a business with advance notice on lead time fluctuations, helping them adjust ROPs accordingly.
A business can tell when their ROP isn’t working if the point regularly triggers reorders too soon or too late. Inventory shortages suggest an ROP is too low, while excess stock and storage space shortages mean the ROP is too high.
More complex ROP formulas use more data. Particularly sophisticated ROP algorithms may be able to use a significant amount of information — including usage, lead time and price trends.
Using Software to Calculate a Reorder Point
While possible, there’s no reason a business needs to calculate its ROP by hand. Automating the process of ROP calculation can make it practical to update the ROP frequently — and may also make it easier to build more complex formulas that take into account as much inventory information as possible.
A business can adopt a stand-alone reorder point control system — which handles calculating the ROP and ordering new stock — or a solution that includes ROP and reordering features.
Inventory management software, MRPs, ERPs and similar tools often contain features that can help a business set reorder points, automate the reorder process and streamline other processes like industrial compliance and sourcing.
Connecting these solutions with sources of important inventory information — including consumption rates, supplier lead times and safety stock levels — can allow for the automation of ROP calculation and the reordering process.
In the near future, it may also be possible to use artificial intelligence and machine learning to generate highly optimized ROPs. An AI-driven solution would also be able to update the ROP frequently, providing managers with a reorder point that is both optimal and highly relevant to current inventory trends.
These solutions may use more information than simpler ROP formulas, allowing for manufacturers to create ROPs that are as useful as possible.
Best Practices for Determining a Manufacturing ROP
The optimal reorder point can be a great advantage when optimizing inventory management for a particular item. If set at the right level, an ROP can help ensure that safety stock never depletes — preventing shortages from impacting a manufacturer’s productivity.
Calculating the optimal level for a reorder point may be challenging, but using existing ROP formulas or formula best practices can help a manufacturer find an ROP that works well for each item.
The right software can make calculating and using ROPs much easier. Many tools and purpose-built solutions for finding ROPs can help any business use these points effectively.
Comments (0)
This post does not have any comments. Be the first to leave a comment below.
Featured Product
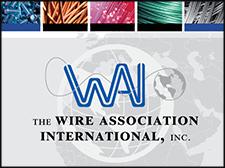