Why Prefab Shops Should Digitize Their Workflows & 5 Entry Points
Widespread prefab construction adoption remains to be seen, but the positive impact these techniques can offer on project outcomes is well-known among construction technologists.
To explain what I mean: McKinsey reported in a May 2023 article that less than 4% of current US housing stock was built using modular techniques. And "only modest growth” was exhibited in McKinsey’s analysis of recent historical growth projections of modular construction in North America. Still, McKinsey’s analysis suggests that modular techniques could “allow home builders to accelerate end-to-end project timelines by 20 to 50 percent while reducing costs by up to 20 percent,” while also making it “easier to execute on urban job sites since they require less space for the storage and preparation of materials.”
And while only 23% of firms reported they were taking steps to improve jobsite performance with lean construction techniques, tools like BIM, and offsite prefabrication (via Autodesk), 90% of firms using prefabrication reported improved productivity, improved quality, and increased schedule certainty compared to traditional stick-built construction (Dodge Data & Analytics). These claims are backed up by data recorded through scholarly research. For example, a study conducted for the International Journal of Environmental Research and Public Health cites prefabrication can cut down on construction waste by 50%, cut down on resources by 35.82%, cut down on health damage 6.61%, and cut down on ecosystem damage by 3.47%. The application of industrialized construction techniques showed an increased growth rate of 16.9% and 8.7%, one study revealed.
While customer acquisition for prefab shops remains a challenge, business owners should focus on refining the message of how prefab can help improve project outcomes through improved quality, process standardization, and timeline and cost reduction; another competitive advantage prefab shops can offer is how they streamline their own internal processes through advanced digitization to offer real-time data sharing and increased collaboration and transparency for customers.
In this article, I explain this point of why digitization is critical for offering customers optimal project outcomes and provide five workflows prime for digitization within the prefab shop.
Why Digitize Prefab Workflows
Manual data entry has the potential to increase risk, yet only 36% of firms have implemented a process for identifying bad data and repairing it, according to an Autodesk/FMI-joint study. What’s more, bad data accounts for 14% of all construction rework, representative of $88.69 billion globally, according to the same study. An Autodesk/Dodge-joint study found similar results with 41% of contractors agreeing that non-standardized data input leads to inconsistent, inaccurate, incomplete, and unusable data.
Digitization can help drive interoperability between processes, from connecting team workflows to stakeholder approvals, and automate daily reporting to reduce opportunities for data inaccurate data to emerge.
Here are five workflows to build digitization into prefab operations:
1. Project Management
When asked “which workflows have improved in 2021,” 42.6% respondents to the ConTech Report from JBKnowledge stated project management, while 58% reported project management to be one of the workflows where workers would most likely rely on a dedicated software solution. The fragmented ecosystem that construction is points scholarly research to the positive impacts of digitization on “construction-phase information management for project owners.”
These include 18 “potential positive impact(s)” with “high agreement rates” among those surveyed:
- Efficiency of documentation
- Contract administration
- Work processes
- Tracking project activities
- Long-term strategic benefits
- Staff's performance
- Documentation in the office as well as on the job site
- Transparency of information on projects
- Document management during construction
- Workflow management and progress
- Communication capabilities
- Financial capabilities
- Construction management in terms of minimizing waste of time and effort
- Construction management in terms of carrying out the right tasks
- Worktime distribution of construction management
- Teamwork cooperation
- Cost savings
- Risk mitigation
Solutions for digitizing the project management workflow include SaaS heavy-hitters like Procore and Autodesk Construction Cloud, who tout cloud-based, “start and finish” platforms that allow teams to connect project stages and manage information in real-time to avoid mistakes. Furthermore, specialty solutions like those offered from e-Sub allow project management digitization specifically built for subcontractors.
Finally, a critical component for success in project management digitization doesn’t stop merely at the implementation of these solutions but working with your technical team to understand possible technology integrations (e.g., project management into ERP, CRM, inventory, design/BIM, etc.) needed for seamless data synchronization.
2. Inventory Management
Inventory management is a critical workflow in need of digitization in the prefab shop, with inventory representing $2,471.6 billion in the manufacturing industry.
Aside from managing the sheer stock levels of raw materials needed in the shop to execute customer project deliverables, digital inventorying also includes keeping track of and maintaining equipment to prevent production-halting equipment breakdowns.
Digitization of the shop’s inventory operations can help:
- Integrate with smart tools to enhance labor utilization and improve quality.
- Track levels of equipment and materials in inventory.
- Integrate into digital twins to visualize production.
- Monitor shop costs.
- Streamline order processing and the customer experience.
- Reduce waste.
- Manage production schedules.
3. Building Information Modeling
Building information modeling has proven quite useful to mitigate risk and prevent expensive rework. But it can also be used to increase collaboration, supporting client engagement within offsite construction, a study from Automation in Construction reveals.
BIM, too, should be integrated with critical team technical infrastructure, such as asset management, to reduce the need for manual reentry of project information, increase real-time information sharing among team members, and improve project outcomes.
4. Smart Tools
Smart tools offer many advantages to the operator and skilled trades that work within the shop to deliver customer project deliverables in a timely manner with exceeding attention-to-detail, craftsmanship, and quality:
- Precision, fully customizable speed and torque settings for application-specific repeatability and specification-level verifiability – users can dial in settings based on their application, save modes to the cloud, and apply across entire equipment inventories.
- Utilization data and reporting – in some cases, users can pull utilization data synced from events performed on tools and roll this data into customizable reports that provide proof of work and verify quality of workmanship and that manufacturers’ specification for critical fasteners were achieved.
- Safety and security – the same Bluetooth® functionality that delivers the ability to customize these tools can be used to crowd-source equipment locating around the shop or help find stolen tools in unfortunate theft situations; what’s more, machine learning makes these tools safer, helping them achieve precise installations more accurately and with less risk to the operator.
5. Digital Twins
Building a digital twin can help mirror shop systems across project lifecycle drawing on real-time data, simulation, and machine learning to help drive smarter, data-driven decisions.
Digital twins can get as granular as “component twins,” helping diagnose malfunctioning parts through IoT sensors, and as macrolevel as process twins providing a view of how your systems work across the entire production facility—and helping you systematically synchronize and maintain peak production efficiency. Equipped with digital twin technology, manufacturing teams were able to reduce rework by 15-20%.
Whereas each of the preceding digitization entry points (e.g., project management, inventory management, BIM, and smart tools in the hands of your production team) represent one component of digitization, the digital twin can represent your entire industrialized construction infrastructure, the mission control of these fully connected workflows across every project stage.
Final Word
While prefab and modular construction have not reached mass widespread adoption, they stand to solve some of the industry’s most challenging headscratchers. In addition to the tremendous positive impacts prefab shops can offer projects from a productivity and quality standpoint, shop owners and teams digitizing their shop operations can provide an even more seamless experience for customers and team members—potentially moving our industry to new heights.
About the Author
Lucas Marshall is a master’s degree-trained professional writer and digital strategist who brings considerable experience creating helpful content for the building trades. At Milwaukee Tool, he’s Content Marketing and SEO Manager, responsible for raising awareness about the company’s digital and IoT products, particularly their connectivity platform ONE-KEY™. In addition to regularly contributing thought leadership to industry publications, he manages, contributes to, and edits the company’s connectivity blog.
Comments (0)
This post does not have any comments. Be the first to leave a comment below.
Featured Product
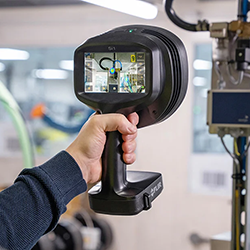