Manufacturers Continue to Look to Courts on Clean Power Plan
New Ultrasonic 3D Printing Process Can Create and Print High-Tech Composite Materials
ATX West - America's Most Comprehensive Design & Manufacturing Event Welcomes Prolific Futurist, Legendary Disney Animator and Philanthropic Innovator to its Keynote Stage
Eyelit Announces the New Operator Certification Module for its Integrated Manufacturing Execution System (MES) and Quality Management Software
Association for Advancing Automation Announces Keynote Addresses for A3 Business Forum
U.S. Cutting Tool YTD Consumption Down 4.1% in November
MesoGlue: Room Temperature Metallic Glue
Opto Diode Introduces Family of Near-Infrared Detectors
SPIE Startup Challenge 2016 semi-finalists announced
Molding Conference 2016 Announces Complete Technical Program
CES 16 - NinjaTek Announces Two New 3D Printing Materials Designed for Industrial Applications
CES 16 - The Possibilities Are Endless with ROBO 3D Creation Machines
MakerBot Announces Smart Extruder+
3D Printing of Motors and Electronics
Robotic Additive Manufacturing Platform for 3D Printing Composite Parts
Records 5446 to 5460 of 5604
First | Previous | Next | Last
Supply Chain - Featured Product
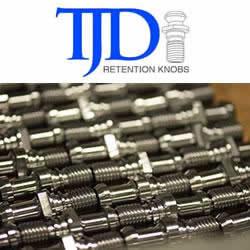