Validation & Quality Control: Optimizing Micro Molding Outcomes
But there is one aspect of a micro molding project that is often overlooked, especially when customers are assessing the in-house capabilities of a micro molding partner, and that is validation and quality control.
The Critical Role of Metrology in Product Development - a Case Study
During the development process, Metronom recognized the critical role of metrology in both R&D and production quality control for its CGM. When working at a scale that is difficult to image with traditional microscopes.
Additive Manufacturing - New Frontiers for Production & Validation
AM has enabled concurrent engineering―where all relevant departments can be engaged early in the product development process. Concurrent engineering replaces traditional "over-the-wall" product development, where design iterations could be delayed by weeks.
METROLOGY & INDUSTRY 4.0
Today's most sophisticated metrology systems drive quality assurance (QA) which has become a fundamental digital task which in and of itself facilitates efficient and cost-effective production processes.
METROLOGY FOR MICRO MOLDING - A CASE STUDY
Eric Felkel, Product Manager, ZYGO Corporation
3D Optical Metrology - Versatile Tools for Today's Advanced Manufacturing
When looking at metrology, general discussion often revolves around the relative merits of contact or non-contact measurement solutions. There is now a drive across nearly all industries for smaller and more complex components.
Automotive Control System Manufacturer Invests in Mulit-sensor Inspection
To upgrade the inspection capabilities of its measurement laboratory, the quality department at the Chassis & Safety division of automotive equipment manufacturer Continental invested in two LK Metrology ALTERA multi=-sensor coordinate measuring machines (CMMs).
Records 1 to 7 of 7
Featured Product
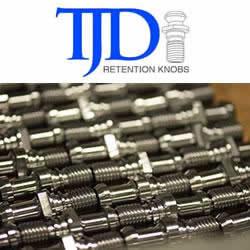
T.J. Davies' Retention Knobs
Our retention knobs are manufactured above international standards or to machine builder specifications. Retention knobs are manufactured utilizing AMS-6274/AISI-8620 alloy steel drawn in the United States. Threads are single-pointed on our lathes while manufacturing all other retention knob features to ensure high concentricity. Our process ensures that our threads are balanced (lead in/lead out at 180 degrees.) Each retention knob is carburized (hardened) to 58-62HRC, and case depth is .020-.030. Core hardness 40HRC. Each retention knob is coated utilizing a hot black oxide coating to military specifications. Our retention knobs are 100% covered in black oxide to prevent rust. All retention knob surfaces (not just mating surfaces) have a precision finish of 32 RMA micro or better: ISO grade 6N. Each retention knob is magnetic particle tested and tested at 2.5 times the pulling force of the drawbar. Certifications are maintained for each step in the manufacturing process for traceability.