VR Welding and the Future of Metal Fabrication
The concerns about VR integration and its health consequences are valid, but it has already proven itself in the world of metal fabrication. It will remain a key part of this industry moving forward.
Spotlight on Fronius Welding Automation - Perfect Symbiosis of Welding Technology and Kinematics
Welding engineers all over the world associate the name Fronius with innovative welding technology. Above all, the innovators are known for providing high-performance, high-tech welding systems.
Ergonomic welding-a contradiction in terms?
There are many ways in which to make the working environment of professional welders as safe and ergonomic as possible, and in doing so positively influence the working conditions and motivation of employees.
Weld Sequencing: Greater Control for Better Results
Digital weld sequencing helps companies to quickly train new welders in times of skills shortages and thereby steadily produce better welding results.
American Welding Society Announces FABTECH 2022 Panel Discussions, Podcasts, Professional Program, Welding Track and Product Discounts
FABTECH returns to the Georgia World Congress Center from November 8-10, 2022, and the American Welding Society is pleased to announce its plans for the event.
Getting Into Automated Welding Without Obstacles
Good welders are hard to find and this problem will get worse in the future. But that's not the only reason why companies with welding departments would like to automate some of their jobs.
How VR and AR are Creating the Next Generation of Welders
By replicating authentic job scenarios in a safe and virtual setting, it's possible to both test and train welders effectively while simultaneously minimizing your long-term cost base.
How Will Labor Shortages Impact Metal Fabrication in 2022?
The American Welding Society estimates a 400,000-worker shortage by 2024. The urgent need for more welders and higher skill levels among welding personnel is widely known and accepted in the U.S. manufacturing industry.
New Laser Welding Process Monitoring Systems Ensure Data Traceability
Ensuring seamless laser weld quality control and manufacturing traceability, the monitors catch weld errors as they occur in real time, instead of reacting to defects downstream. This ultimately increases yield, improves quality, saves labor, and increases savings.
Stud Welding: What Is It And What Are The Benefits?
Should you be using stud welding in your metalwork?
ManufacturingTomorrow - Special Tradeshow Coverage
FABTECH 2018
FABTECH takes place in Atlanta, GA November 6th - 8th. This ManufacturingTomorrow.com Special Tradeshow report aims to bring you news, articles and products from this years event.
zenon helps Novarc Technologies optimize HMI user experience
Novarc Technologies Inc. creates robots for spool welding and other custom welding operations. To enhance the operator experience, Novarc turned to COPA-DATAs zenon to create a simple user interface for its robotic welding machines.
New Laser Sources Improve Battery Performance by Enabling Dissimilar Metal Joining
Using aluminum and copper for battery tab to cell welding improves electrical efficiency and battery module/battery pack performance.
Projection Welding of Fasteners to Hot Boron Stamped Components
There are a number of manufacturing issues that come up when projection welding fasteners onto hot stamped boron steel components. In most cases, the weld nuts and studs used are considerably softer than the 1500 MPa stamping.
Robot welding: More efficiency for programming and equipment fabrication
Crown relies on FASTSUITE Edition 2 for offline programming of robotic welding cells.
Records 1 to 15 of 16
Featured Product
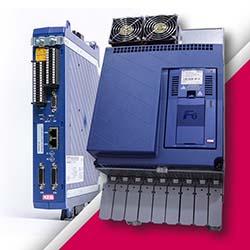
KEB VFDs for High Speed Motor Control
KEB's VFDs are the key to unlocking peak performance in your high-speed machinery. Engineered for precision control, even without feedback sensors, our F6 and S6 drives utilize advanced software and high-frequency output. This ensures smooth operation, reduced vibration, and optimal efficiency. Whether you're building turbo blowers, power generation systems, or other high-speed applications, KEB VFDs deliver the reliability and performance you need.